50 years of people and steel processing
Half a century of operations was celebrated on 3 November 2022 at the home of BlueScope’s Victorian COLORBOND® steel manufacturing site at Hastings. The 50th anniversary of BlueScope’s Western Port operations is a significant milestone for BlueScope and the Australian steel industry.
Western Port’s original company, Lysaght, took its name from the Irish born founder, John Lysaght, who established a galvanising works in Bristol, England in 1857. Lysaght was the pioneer of many modern steel coating technologies and had built-up a good business selling galvanised iron as a building material throughout Australia in the second half of the 19th century.
By 1913, Lysaght’s Galvanised Iron Pty Ltd was turning over 85,000 tons annually, which was around 70 per cent of the English company’s output. It was also coincidentally around 70 per cent of the Australian market for galvanised iron.
In 1918, John Lysaght (Australia) Pty Ltd was founded as a wholly owned subsidiary of John Lysaght Ltd of England.
By 1921, Lysaght began rolling and galvanising sheet steel in their first Australian rolling mill and galvanising line, to serve the Australian building and construction industry in Newcastle. Feed material for Lysaght’s Newcastle works was from the adjacent BHP steelworks, establishing an enduring link that would ultimately see the two companies become one.
Barely six years after Lysaght commenced operations in 1921, by 1927 the Newcastle plant had doubled in size, and by the end of 1933 it had reached its maximum planned capacity. The expansion to Port Kembla followed, and with it, new technology to replace the original Newcastle plant, which closed completely in 1966.
At the same time, works were in the pipeline by the Hoskins family to operate a steelworks facility in Port Kembla, New South Wales. Led by Charles Hoskins, Australian Iron and Steel Limited (AIS) soon became one of the most profitable steel companies across the country. Meanwhile, the Broken Hill Proprietary Company Limited (BHP), which had been founded in 1885, had also shifted into steelmaking.
By 1935, the Great Depression had impacted steelmakers and Australian manufacturing. The tough economic environment was the catalyst for the merger between AIS and BHP. This led to BHP acquiring the Port Kembla facilities, and iron ore deposits in Yampi Sound, Western Australia. The company soon grew into the largest integrated steelworks in the former British Empire. In 1961 John Lysaght (Australia) became a public company by issuing three million shares (20 per cent) to the Australian public. In 1969 BHP acquired 24 per cent of John Lysaght (Australia).
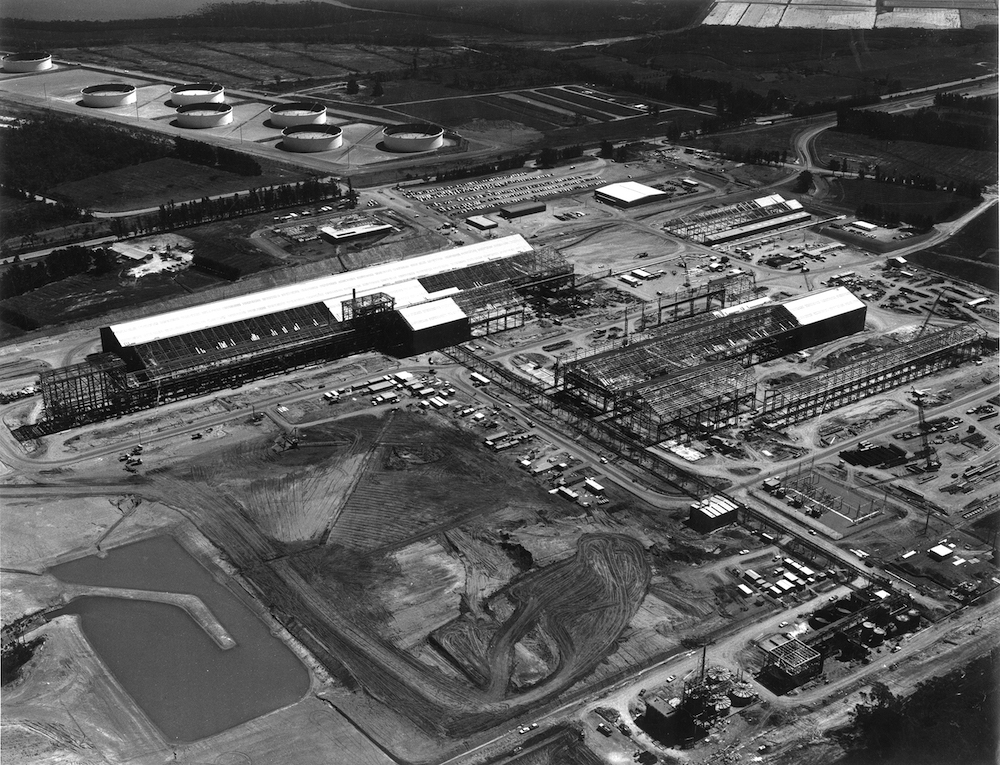
Plans for expansion
By 1967, Australia had become the largest producer and consumer per capita of galvanised steel. By the end of the 1960s, Lysaght was supplying a wide range of products to meet the requirements of customers in many industries, and was also exporting to a sizeable market in the Pacific and South East Asia.
The vital decision was whether to build a new plant at Port Kembla, with its inherent advantages of location close to the existing infrastructure of the steel plant, or to search for a new site with added advantages, including potential opportunities to expand.
In 1968, a feasibility study was undertaken jointly between BHP, John Lysaght (Australia) and Guest, Keen and Nettlefolds, resulting in an agreement for the development of a comprehensive new sheet steel production and processing plant. The joint venture being accomplished through John Lysaght (Australia) Limited.
It was decided that a new site for sheet and coil steel production would need to offer the opportunity for expanding into the manufacture of basic steel in the long term. The major location factors to be considered for an integrated steelworks included raw materials, markets and transportation. A site with deep-water frontage and availability of water, power, fuel and workforce access was also of vital importance.
Potential sites were identified in New South Wales, Victoria, and South Australia. John Lysaght, together with engineering director, Clive Shegog, had previously embarked in 1966 on exploring the suitability of each site. The site on Western Port Bay was chosen after much investigation.
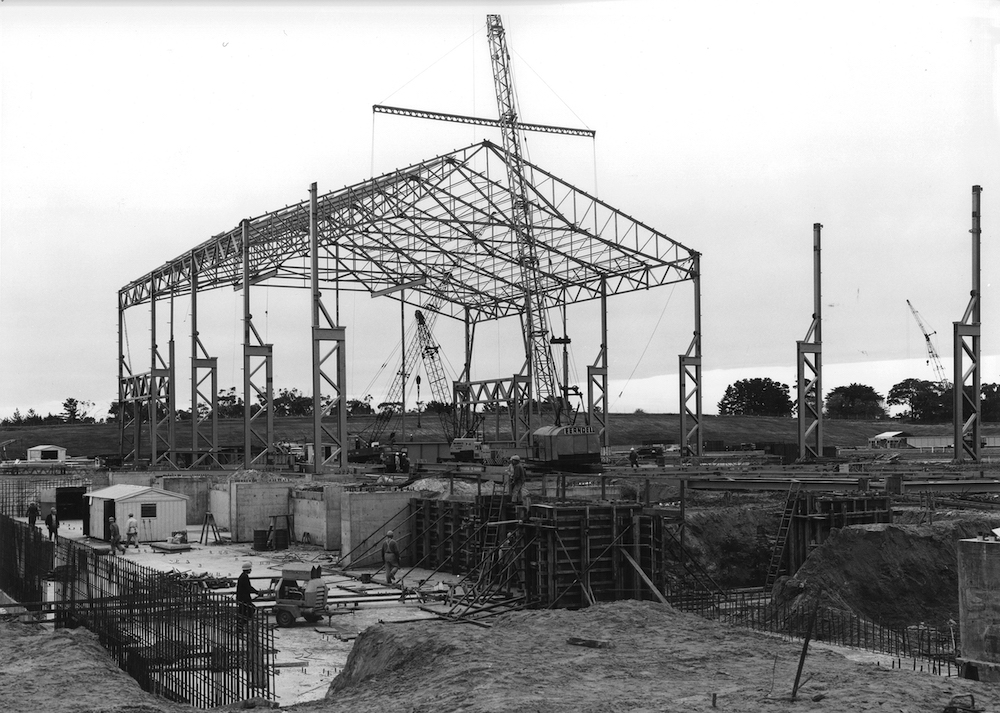
Community consultation
As the site of the future steelworks was to be in a quiet and largely rural area, John Lysaght (Australia) went to a great deal of expense and effort to assure the local community that they were working to protect the local area.
The company believed communication was the key to this and made every effort to ensure construction was as transparent as possible with the local community. Part of the company’s commitment to community engagement included the original Lysaght establishment in Hastings, the ‘Lysaght Information Centre’. The Lysaght Information Centre was set up in the main street of Hastings, and opened in October 1970, during the early stages of construction.
It aimed to keep any and all interested parties informed, which included conservationists, environmentalists, businesspeople, potential employees and school children from virtually every local school in the area. The Centre included scale models of various parts of the plant along with full site layouts and the wharf area. A public viewing area and platform were also created, so the general public could see from an elevated position the construction progressing.
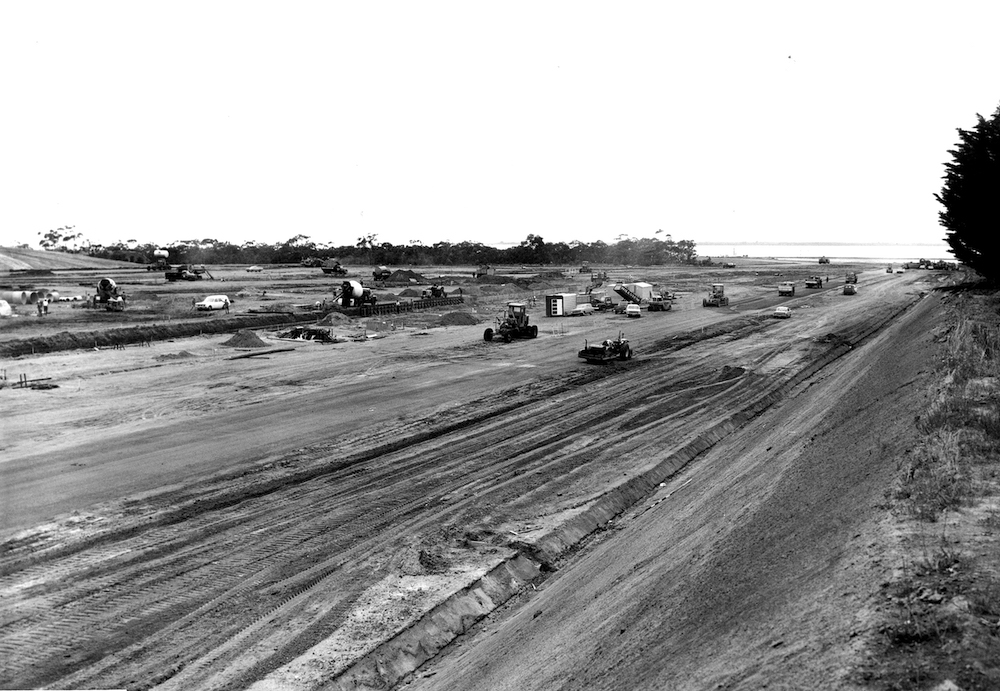
Legislative approvals
One of the attractions for the planners at John Lysaght (Australia) to the Western Port site was that it is Victoria’s only natural deep water port, and one of the few in Australia. However, prior to the early 1960s, there was minimal industrial development at Western Port. This was soon to change, and its development was controlled by various Victorian Government acts.
The Western Port (Steel Works) Act 1970, and the Western Port Steel Works (Development Control) Act 1970 provided for the ultimate establishment of an integrated iron and steel industry, along with the necessary wharfage by John Lysaght (Australia), with all dredging being provided by the State. Initial dredging in 1971–1972 removed around 700,000m3 of material to clear the approach channel and swinging circle. By 1981, the State had spent over $1.62 million on dredging for the Western Port steel site.
Three stages of construction
Construction of the Western Port development was planned in three main stages:
- Cold strip plant (1970-1973) with $92 million budgeted
- Hot strip mill (1974-1978) with $160 million budgeted
- Blast strip furnace and steel production with $750 million estimated
Plans for the construction of the new steel plant were to be in two major stages. The cold strip plant to be the first stage, and the hot strip mill the second stage. Notably, these plans were prepared even before the final site and layouts of the works had been determined.
To support the initial cold strip plant, it was anticipated 10,000 tonnes of hot roll coil feed would be required each week, which was equivalent to two ship loads.
Despite the hot strip mill being the preceding stage in the production process, construction of the Western Port hot strip mill was planned to be the second stage of the Western Port plant. The reason for this was because there was still sufficient surplus hot strip mill capacity in Port Kembla at that time. Thus, by delaying the construction of the Western Port hot strip mill until after the cold strip plant, the additional capital outlay could be deferred until Port Kembla hot strip mill capacity had been saturated.
Operating lines were to be planned to allow for continued expansion in outputs, and this is shown on original drawings. Multiple site layouts were proposed, which included a fully integrated steelwork plant, as a third and possible final expansion stage. Of note, there was no inclusion of any paint line in the initial Western Port site layout plans.
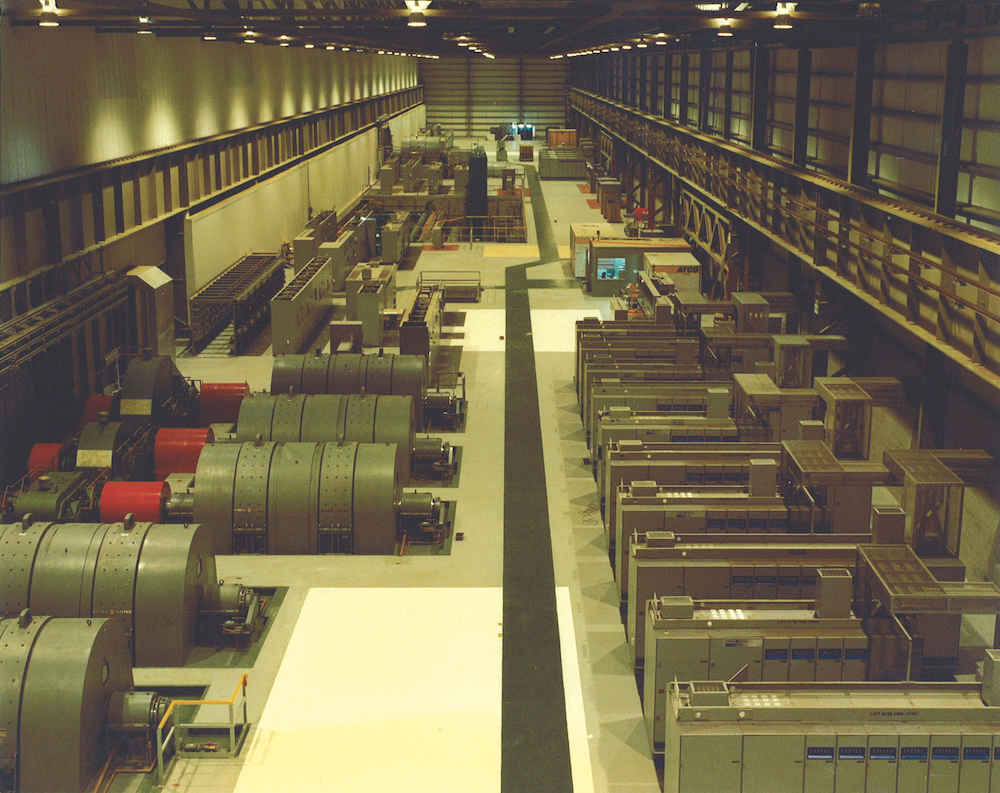
Cold strip plant
In April 1967, work commenced at Western Port with initial site sampling. Sampling revealed that there was clay and sand down to a depth of at least 73m, and thus no suitable bedrock at a reasonable depth to anchor foundations for the heavy machinery. This meant all foundations for both buildings and equipment had to be designed without any support piles. Luckily, the soil at the site had excellent bearing capacity. So, even without piles, the foundations could be designed in the concrete raft style, effectively ‘floating’ on the soil.
It was not until April 1970 that the first site levelling commenced, which took six months to complete. The foundations required approximately 70,000 cubic metres of concrete to be poured, which contained around 4,000 tonnes of reinforcing steel. During construction of the cold strip plant, over 900 personnel were employed from more than 30 different companies.
Throughout 1972, key personnel were transferred to Western Port from other Lysaght plants to assist with commissioning and training operating crews. Of the approximately 600 personnel employed at Western Port for the initial start up, around 80 were existing Lysaght personnel. The remainder of the personnel were mostly recruited locally and trained on the job.
By the end of 1972, the plant was rapidly nearing completion. In November 1972, metal coating line four was commissioned, and the first delivery of galvanised coil was made to customers. December 1972 saw production of the first cold reduced coil from the five stand mill. In February 1973, start-up of the pickle line commenced, with the cold strip plant commissioned in March. In April, the coil annealing and coil temper mill started up.
Although construction of coil paint line two started later than the rest of the cold strip plant, it commenced production in November 1973. This was driven by the huge demand for COLORBOND® steel, which the company was keen to capitalise on.
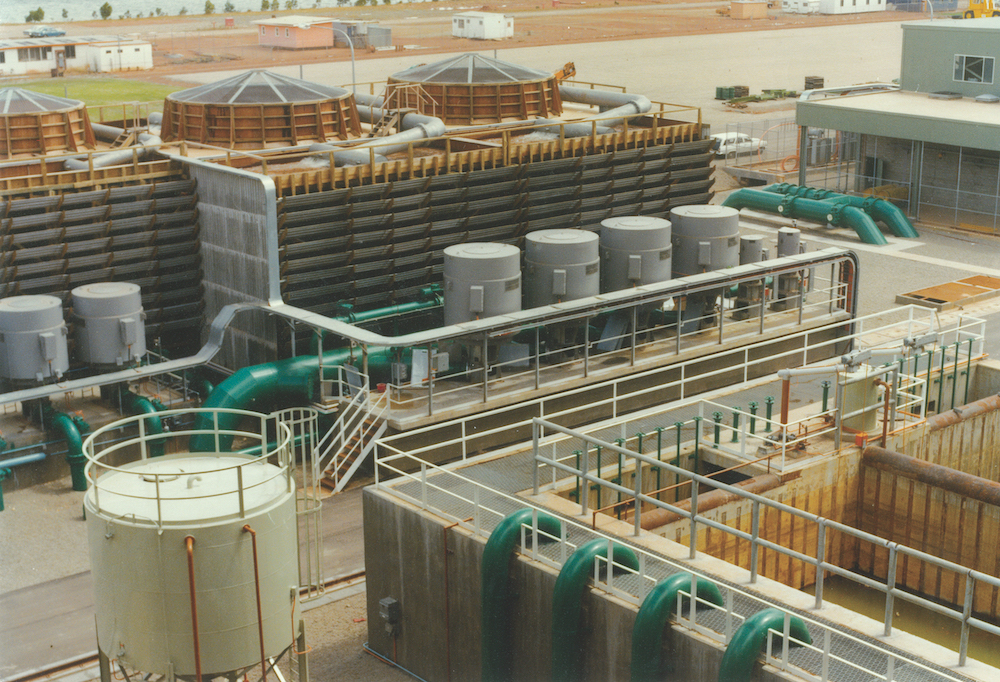
Hot strip mill
Following the successful implementation of the cold strip plant, work began on the construction of Victoria’s first, and Australia’s second, hot strip mill.
Earthworks commenced in April 1974, with construction plagued by several strikes and delays over various industry issues. By December 1974, most of the earthworks were completed, with roadways and pavement storage areas in progress. By July 1975, a new construction phase had commenced, with the first building columns erected for the southern wall of the roll shop.
The foundation contract involved pouring approximately 60,000 cubic metres of concrete. By the end of 1975, the building frame for the hot strip mill was 80 per cent complete, with erection of the secondary steelwork commenced. There were approximately 7,000 tonnes of steelwork required for the hot strip mill buildings. Construction of the basement slabs and building piers were also well-advanced, as were the foundations and footings. Sheeting had also commenced on the roll shop, and the crane for the roll shop had been erected; at 100 tonne capacity and with a span of 36m, this was one of the largest cranes on-site.
By mid-1976, the 60m high furnace stack was erected, and much of the wall and roof cladding was installed. The furnace walking beam support beam charging end plate was in place and foundations were complete. In early 1977, the mill housings began to arrive on-site and the first of the 133 tonne finishing mill housings was erected into its shoe plates. Another four followed quickly after. In February 1978, the hot strip mill underwent commissioning.
At 1:58am on 9 March 1978, the first successful prime coil to make it through the complete hot strip mill process was run (output coil number AA006). The five prior coils cobbled or had other issues.
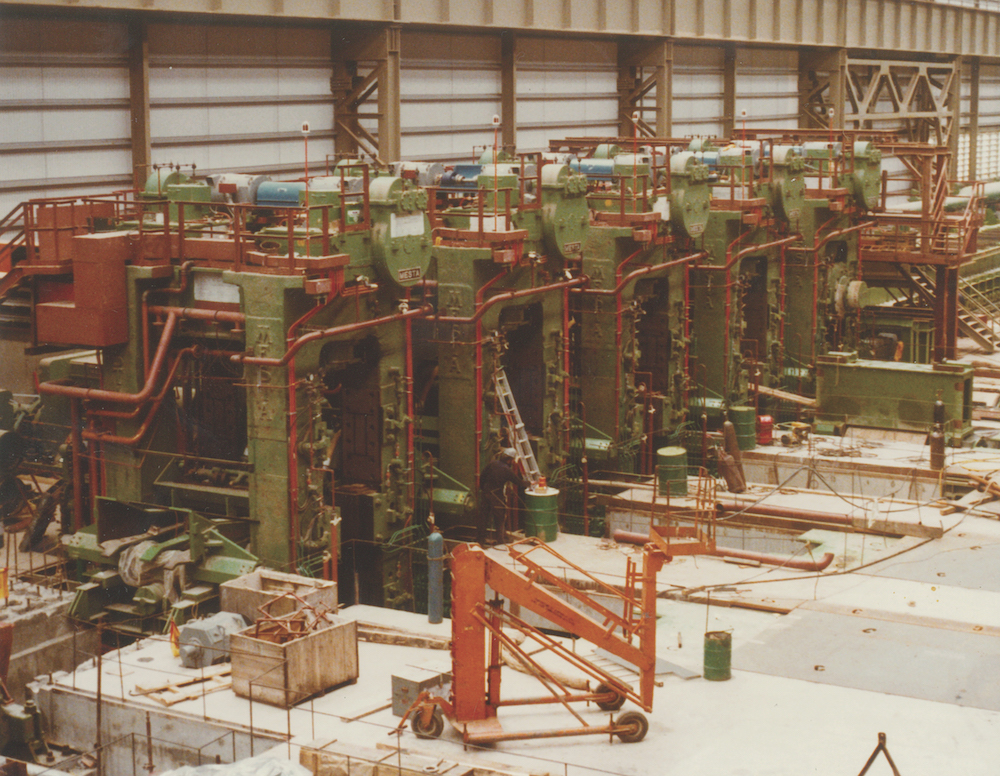
Zincalume® and Colorbond® demand on the rise
Following the introduction of Zincalume® steel into the market in 1976, Lysaght could not keep up with demand for COLORBOND® with their existing three paint lines. So, capital investment was approved to expand Lysaght’s COLORBOND® steel capacity by 150,000 tonnes per annum to around 400,00 tonnes per annum.
Civil works for metal coating line five commenced in June 1978, with construction underway by mid-August. Construction continued on schedule, with all foundation work complete, housing and framework installed, line equipment installation underway and the zinc pot in position by May 1979. Metal coating line five was commissioned in December 1979 and officially opened on 13 May 1980.
Not long after, site works for coil paint line four commenced. The paint line drum storage area was expanded in late 1981 to cater for the increased paint supply required. By the end of March 1982, the coil paint line was in a ready-to-run state and was commissioned. The official start-up on 29 September 1981 was attended by over 180 guests.
The 1980s and 1990s witnessed several developments at Western Port. In 1990, the tension leveller roil line was commissioned, as was the electrolytic cleaning line. In 1992, metal coating line six was commissioned. The following year, metal coating line four was converted to Zincalume® steel.
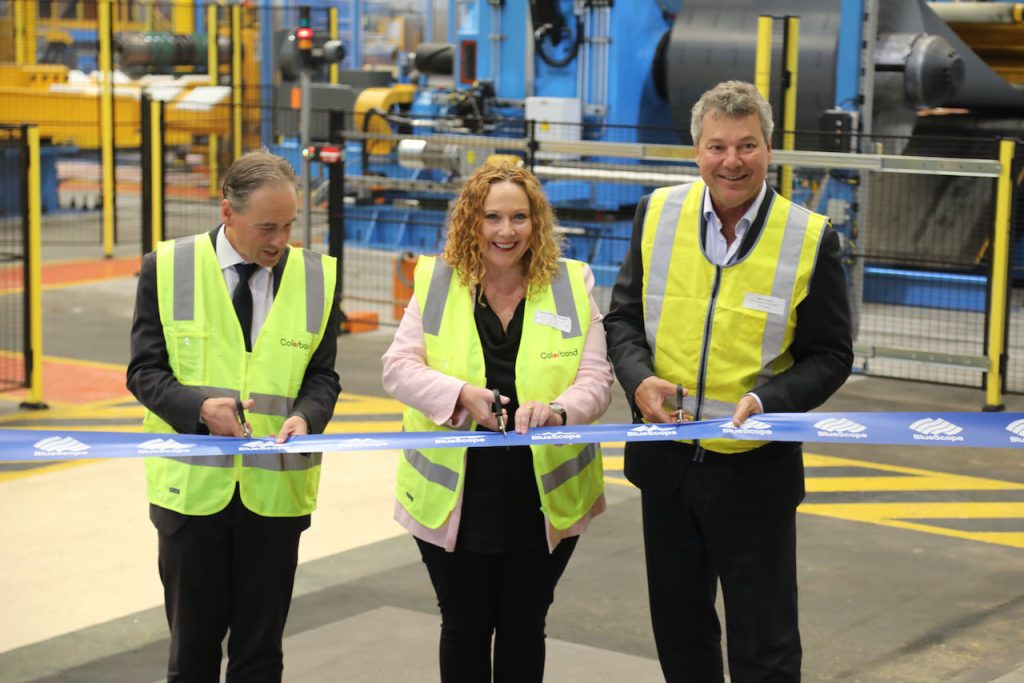
A remarkable achievement
Today, BlueScope is the largest private employer on the Mornington Peninsula. More than one million tonnes of steel products such COLORBOND® steel, ZINCALUME® steel, and TRUECORE® steel are made at Western Port each year, destined for national and international markets.
Michael Hussey, the plant manager at BlueScope Western Port, said 50 years of operations on Victoria’s Mornington Peninsula is a remarkable achievement. “BlueScope Western Port, which opened under the name John Lysaght Australia in 1972, currently employs around 800 people from the region, however, over the last 50 years, I’m proud to say we have employed around 10,000 people.”
“I’m immensely proud to be the Western Port Manager and work with such great people, many of whom I call my friends. When I reflect on what we have achieved over 50 years and the strength we possess at Western Port today, I am very confident that we can deliver on all of this and more into the future.”
“Challenges will be met and overcome, opportunities will be taken and leveraged further, our sustainable future is in our Western Port team’s hands (and the team members who will follow us) and is clearly achievable,” Hussey said.
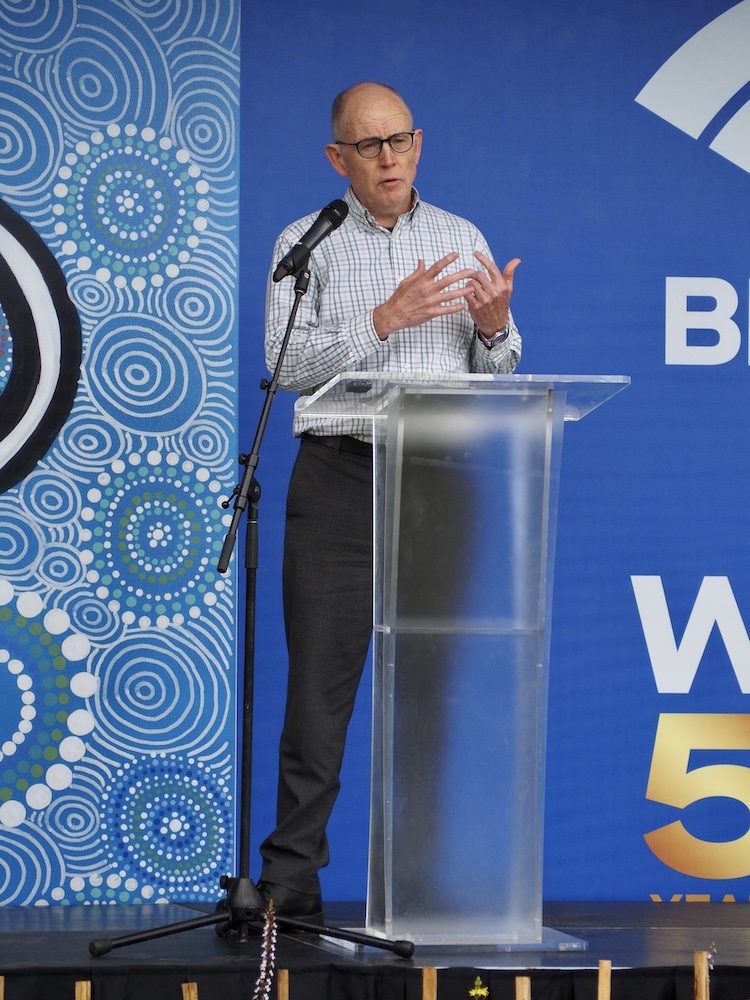
Moving ahead: looking at new horizons
BlueScope has laid out the foundations for the next 50 years at the Western Port facility. In March 2022, a $34 million service centre was opened.
BlueScope’s managing director and chief executive officer, Mark Vassella, said the centre uses the latest technology, secures local jobs and strengthens Victoria’s manufacturing industry. “This new facility, with capacity in excess of 100,000 tonnes per annum, consolidates BlueScope’s steel processing capabilities in Victoria on one site, using the latest technology and with a clear focus on our customers, safety and the welfare of our people.”
It features an automated slitting head build robot, which is the first of its kind in Australia. It can construct a slitting cutting head to individual customer requirements without manual intervention from operators or other tradespeople.
“It also helps keep BlueScope people safe at work by eliminating manual handling and other safety risks,” Vassella said.
Source
Paul Reville, The Western Port Story: 50 Years of Our People and Steel Processing