In today’s industrial landscape, optimising steel production schedules is crucial for navigating volatile energy prices.
Fluctuations in energy costs can significantly impact operational expenses, making it imperative for businesses to devise strategies to mitigate these costs. GridBeyond examines how technology can support businesses in minimising the impact of energy price peaks, ultimately reducing production costs by scheduling operations against energy prices.
Finding flexibility
Electricity prices exhibit intra-day variability due to a complex interplay of supply and demand fundamentals, renewable energy integration, fuel costs, and weather influences. Prices can fluctuate within a day due to changing patterns of electricity consumption, the availability of different generation sources, and overall market conditions.
Market mechanisms, such as real-time pricing and incentive programs for demand response, encourage consumers to utilise the flexibility in their operations and modify generation and consumption patterns in reaction to external signals to provide a service within the energy system. For example, a consumer might schedule production away from periods when electricity prices are at their highest.
At the site level, energy flexibility means reducing energy use or shifting that usage to different times. Organisations that leverage their energy flexibility can earn new revenue and reduce energy bills by avoiding high-priced hours or capitalising on grid programs and incentives.
The reduction in energy spend from unlocking your organisation’s energy flexibility can be significant.
But on sites where specific parameters must be adhered to, digital twins allow for a tailored approach to finding flexibility embedded in processes or assets, enabling more informed decision-making in creating a more efficient and cost-effective energy strategy.
Case study: steel manufacturing
In this example a site in the steel manufacturing sector was using power to operate throughout the day, despite the cost of power fluctuating across settlement periods.
While the site had a series of fixed asset parameters, flexibility was found in the Electric Arc Furnace (EAF) and turbo blowers without impacting overall product quality or operations – providing an opportunity to make cost savings on electricity and generate revenue for the business.
By utilising the variable speed drive motors in the turbo blowers and the temperatures of the EAF and using Robotic Trading, energy flexibility was traded in the highest revenue markets.
This meant the site earned revenue from flexibility offered in grid programmes in addition to avoiding the peak price power periods and reducing overall production costs. Production from the remainer of the operational process was not impacted as these assets were classed as fixed asset parameters with hard constraints of operation.
Results: By forecasting market prices, shifting load, and trading, GridBeyond’s solution saved $3,694,827 annually, accompanied by a substantial reduction of Scope two emissions.
This article was supplied as part of a paid advertising package.
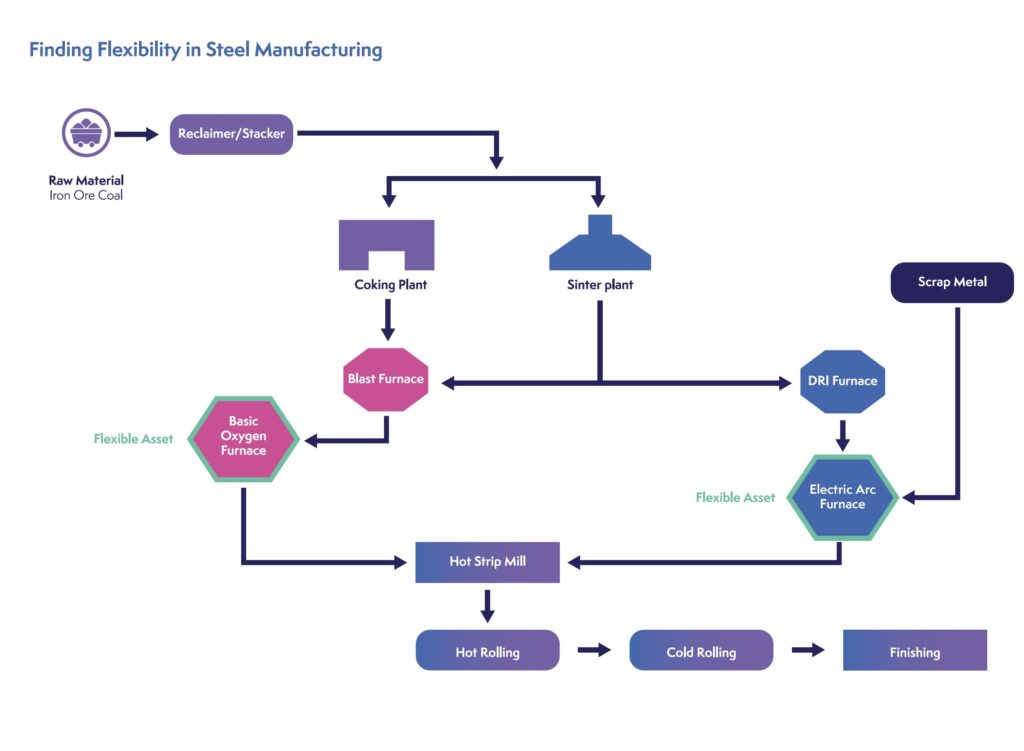