Enduraclad has emerged as Australia’s fastest-growing wear plate manufacturer, offering high-quality products such as chromium carbide, ceramic, and steel components to the global resources sector. In just over a decade, the company has transitioned from a humble start in Jason Kell’s garage using borrowed equipment to a global frontrunner in wear plate manufacturing. The key to this meteoric rise? A commitment to innovation, quality, and above all, its people.
Enduraclad is Australia’s fastest-growing wear plate manufacturer of high-quality products, supplying chromium carbide, ceramic and steel components to the global resources industry. Starting with borrowed tools just 12 years ago, the company has kept a steady focus on innovation and reliability – enabling resource businesses to reduce the wear and tear on their material handling machinery.
Now sought out by mines around the world, Enduraclad’s range has grown to meet the strong demand for premium products managed to world-class standards. But according to founder and managing director Jason Kell, the company’s secret ingredient is its people.
“Anyone can produce what we do,” Jason said. “However, it’s the culture that is led into the team that makes it successful. On top of this, Enduraclad makes really good quality products. We take great pride in making something better than what we have done in the past.”
From humble beginnings to industry leader
Looking at Enduraclad’s position as a global leader in its field, it is hard to believe that the company began in Jason’s home garage in 2011 with equipment he didn’t even own. “I started this business to fill a gap in the mining wear parts industry,” Jason explained.
Recognising that clients were often waiting months for products to be manufactured, Jason saw an opportunity to deliver an urgent supply of mining wear parts. “Many items I could produce myself within two to three days,” he said. “The mining clients were waiting six to eight weeks from the current companies providing the same products.”
Today, Enduraclad is a leading provider of Australian manufacturing wear resistant products used in mining and civil applications. From its original staff of one, the company now employs 80 people in four locations across Western Australia, as well as a 10-person team in its Queensland branch. Enduraclad’s range of premium products include extra thick chrome carbide and tungsten carbide overlay products.
These have a long life span of up to three years in many mining applications, where previous products only lasted
a year.
“Enduraclad is considered a supplier of choice to Australian and worldwide mining clients. We manufacture wear resistant products which protect mining assets from abrasion, impact, and corrosion – giving the asset a much longer life span than it would without protection,” Jason said.
Putting people first
Behind Enduraclad’s products is a dedicated team of employees determined to produce bigger, better, and faster manufactured items to meet a growing need. As the business continues its rise to the top, Jason firmly believes that it is only as strong as the people who make up its team.
“Each team member has contributed to Enduraclad’s success,” Jason said.
That’s why he works hard to foster a positive working culture that draws his staff closer together, and enables them to thrive professionally and personally. “Simple things like monthly barbecues for time out and socialising are important in the business, as well as encouragement for work/life balance.”
Employees enjoy additional benefits such as flexible working hours and work from home arrangements. They also have permission to get outside and walk or jog for 30 minutes during paid hours, whether on the day shift or night shift, as an opportunity to exercise or simply refresh the mind.
In the workplace, everyone is encouraged to contribute their ideas, with rewards often given out for the best ones as well as monthly employee recognition. The end result is that every team member feels comfortable speaking out and feels that they are heard.
“Staff feel relaxed enough to approach management at all times with issues they may have,” Jason said.
Enduraclad is also an avid supporter of providing opportunities to people with disabilities, developing employment and training programs to break down barriers to entry in the workforce.
“I believe disability is just a label,” Jason said. “Everyone has skills that are valuable, it is just a matter of matching their skills to the working environment. We have actively sought to improve Enduraclad International’s training programs with the aim of employing more people with disabilities.”
Driven by a passion for innovation
To support its growing operations, the company has built world-class manufacturing facilities equipped with the latest technological advancements. In addition, the fabrication facility hosts 75 tonnes of overhead cranes which allow the team to take on very large projects.
“Enduraclad has modernised robotic equipment to manufacture its products. Designed by myself, the machines are well-equipped to run autonomously as required, helping to reduce the labour component to operate the business,” Jason said.
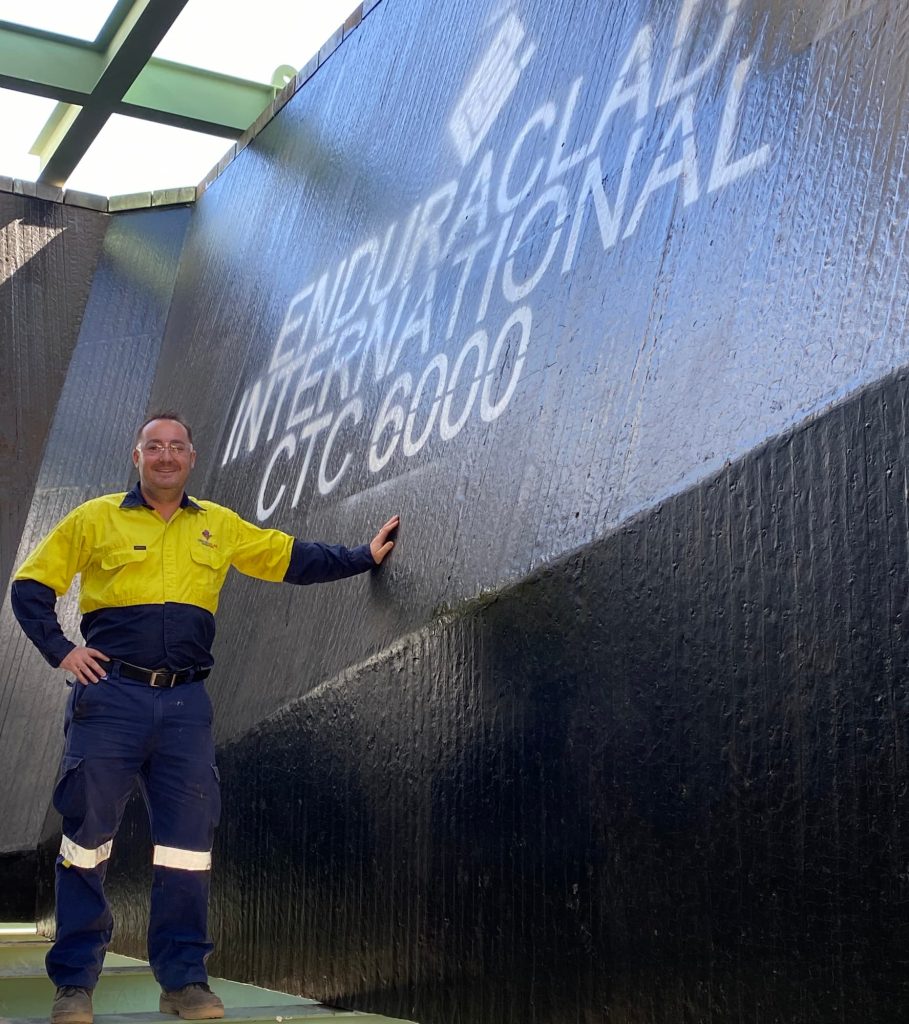
From the outset, Jason was clear that he wanted to have more than one piece of each critical equipment asset – to prevent the possibility of breakdowns slowing down production.
“We now host a multitude of each of our major manufacturing pieces, much of it surplus to daily needs,” he said. “However, it’s been extremely handy when we have to ramp up operations quickly for a project.”
This same passion for innovation and creative problem-solving is the driving force behind Enduraclad’s premium product range. As an example, the team identified an issue in the design of many mining chutes, with hundreds of small liners that are bolted into place. This results in many days of shutdown time to remove and replace the liners when they become worn out.
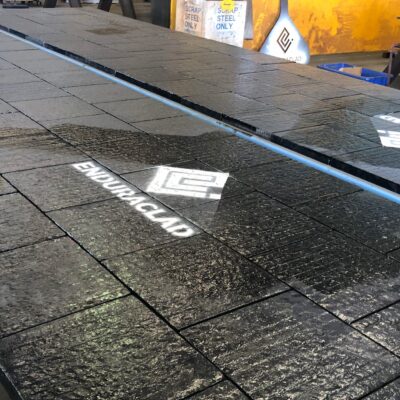
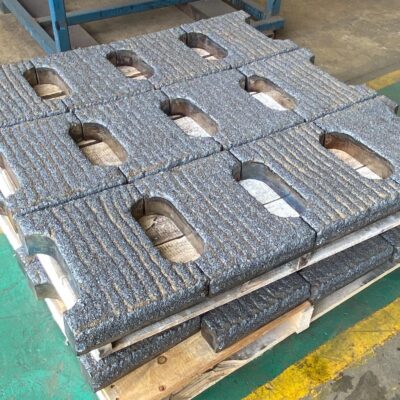
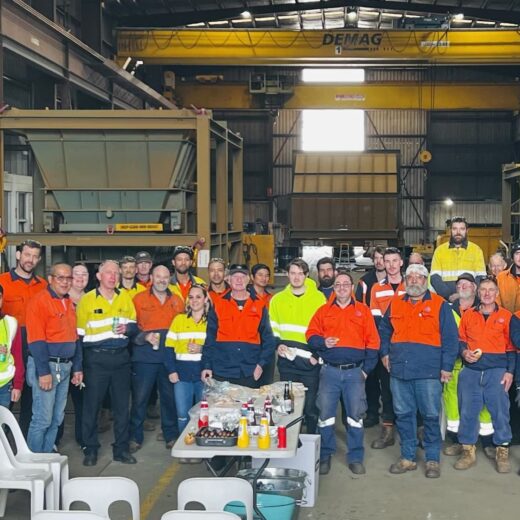
“Enduraclad produces the world largest liners, allowing us to design and manufacture full tubs as liners inside existing chutes. This eliminated hundreds of smaller liners and allows shutdowns to occur in one day or less,” Jason said.
One of the company’s most popular products is CTC-X® or cemented tungsten carbide. Uniquely manufactured by Enduraclad, it is swiftly gaining a reputation across the industry for its outstanding results in mining port applications. CTC-X® is the super extreme in wear resistant liners and is designed for applications that experience severe abrasion, where standard wear plate is ineffective.
“Where alumina ceramics were once used, the CTC-X is withstanding impact and abrasion to allow port chutes to last more than a year in service,” Jason said.
CTC-X® is available with cemented tungsten carbide and cobalt tiles, in a range of thickness up to 20mm, vacuum brazed to a mild steel backing plate.
Another premium product offered by the company is EnduraCoat™—a tungsten overlay developed to provide a cost-effective solution in prolonging the life of applications and equipment subject to extreme wear. Enduraclad’s unique welding process incorporates layering tungsten chips to a base metal allowing for a greater life cycle, typically outlasting regular overlay plate by as much as 10 times. EnduraCoat™ can be applied in thickness up to 15mm.
Their TiC™️ titanium carbide wear liners comprise of a TiC™️ insert, moulded in a high-tensile strength natural rubber matrix, and mounted on steel backing plates. All rubber ceramic liners are hot vulcanised together using specialised equipment which provides a bond strength that exceeds the tensile strength of the natural rubber matrix.
As a result, the TiC™️ insert will remain in the rubber matrix, offering consistent wear and impact protection across the entire life of the liner.
Enduraclad also supplies a range of quenched and tempered steel plate. With four large profile cutting tables, Enduraclad can cut shapes from 1mm up to 200mm thick. With the option of oxy and plasma bevelling, Enduraclad regularly repairs base lips and edges.
Winning top industry honours
After only a few years of operation, Enduraclad was already garnering industry accolades – winning the medium business category in the Western Australia Telstra Business Awards.
Enduraclad has gone on to receive more honours, including the nationally-recognised SME Business of the Year in the Telstra Business Awards in 2017, and Optus Manufacturing Business of the Year for 2018. To complement these wins, the company was also selected for the Regional Business Awards in 2015, 2017, 2018, and 2019.
But for Jason, this recognition is a testament to his team. “They are all well-deserving recipients of these awards,” he said.
Enduraclad’s journey from a small start-up operating out of a garage to a global leader in wear plate manufacturing is nothing short of remarkable. Through a commitment to innovation, product quality, and an employee-centric ethos, the company has carved out a significant niche in the global resources industry. While its state-of-the-art facilities and pioneering solutions like the world’s largest liners have set industry standards, it’s the company’s investment in its people and inclusive practices that truly set it apart.
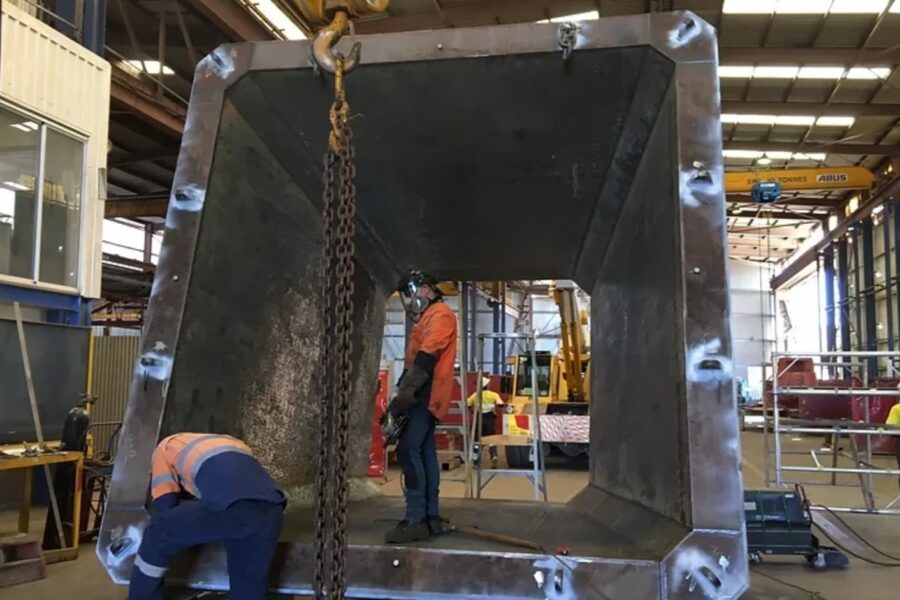
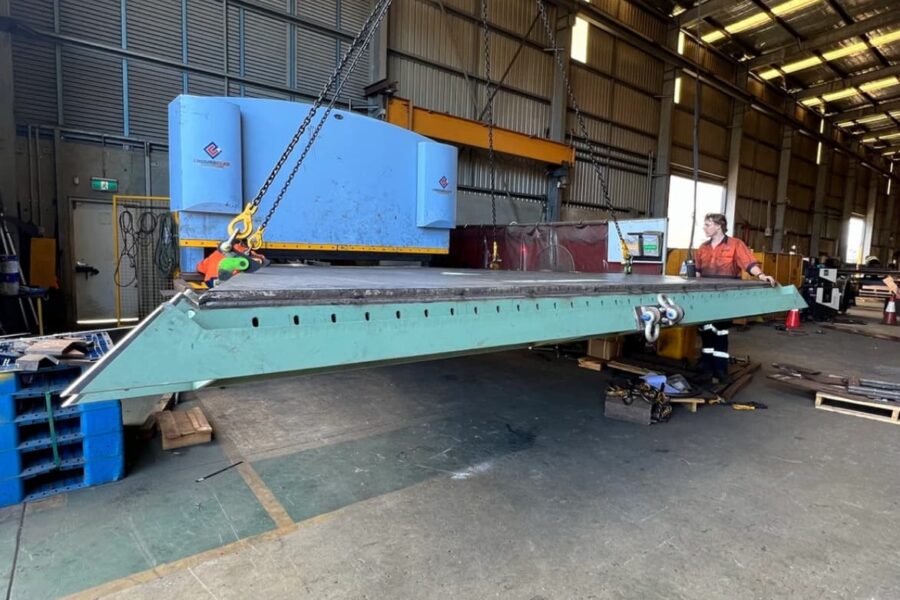
Product profile: Enduraclad weld overlay solutions
Manufactured to world-class standards under strict Australian safety guidelines, Enduraclad’s range of welded overlay liners is amongst the industry’s best globally.
ECI60®
Used widely amongst civil and earthmoving applications, EC160® is the right choice for general overall performance in just about any application. It’s readily available in a variety of thicknesses and it’s easy to process finished products yourself with minimal equipment.
ECI80®
As the impact specialist, ECI80® is a quality grade CCO wear plate suitable for high wear areas. Expected to last up to three times that of standard D60 plate of equal thickness, it has excellent impact and abrasion resistance – taking the bump and grind in one effort.
EMEX®
EMEX® overlay can be applied direct to shaped items as well as to standard base material such as mild steel plate of varying thicknesses, ensuring the finished parts are readily weldable. Alternative base plate grades can be incorporated with the EMEX® overlay to meet specific customer requirements.
CTC6000®
CTC6000® is the super extreme in wear-resistant wear plate and is designed for applications that experience severe abrasion and moderate impact, where standard chromium carbide wear plate is proving ineffective. Customised to suit each application, CTC6000® is the ultimate choice when it comes to resisting wear.
ECI MAXI®
ECI MAXI® is the super extreme in wear-resistant wear plate and is designed for applications that experience severe abrasion, where standard wear plate is ineffective. Tungsten Carbide granules are spread through a tough matrix of Ni, Si, B, producing high hardness resulting in significant increases in service life over other standard overlay wear plate.
Superflow®
Superflow® is Enduraclad’s answer for promoting material flow and minimising friction. This material, ingeniously produced by our proprietary machine, comes in ‘smooth’ and ‘polished’ finish surfaces. The polished surface creates a virtual non-stick surface preventing hang up of sticky products in many applications.