In 2020, BHP Mitsubishi Alliance (BMA), a 50:50 joint venture between BHP and Mitsubishi Development, engaged Civmec to fabricate, modularise and commission a 2,000 tonne shiploader (SL2A) for the Shiploader and Berth Replacement (SABR) project at Hay Point Coal Terminal.
Located at the Port of Hay Point, 38km south of Mackay in Queensland, the Hay Point Coal Terminal is capable of handling more than 55 million tonnes of coal for export every year.
To improve cyclone immunity and ensure the long-term sustainability of Hay Point Coal Terminal, BMA initiated the Shiploader and Berth Replacement (SABR) project. The project scope includes the disassembly of the existing Berth 2 and Shiploader 2 and the fabrication and installation of new Berth 2A and Shiploader 2A structures at the Hay Point Coal Terminal.
Aurecon Engineering was responsible for the design of the new Shiploader 2A and new Berth 2A infrastructure, which focused on improving the severe weather rating of Berth 2A to be consistent with Berth 3 and associated infrastructure that was commissioned in 2015.

About the Hay Point coal terminal
The Hay Point Coal Terminal is a part of the BHP Mitsubishi Alliance (BMA), the 50:50 joint venture between BHP and Mitsubishi Development. Capable of handling more than 55 million tonnes of coal for export every year, the Hay Point Coal Terminal is located at the Port of Hay Point – 38km south of Mackay, in Queensland.
Established by a joint venture between Utah Development Company and Mitsubishi Development in 1969, Hay Point was originally built to service the Goonyella and Peak Downs mine sites. Hay Point saw their first coal loaded in 1971 – with just a single berth, shiploader and crawler mounted reclaimer and stacker.
A second berth was added in 1975. In 2006-2007, a two-phase, $256 million expansion project increased the
capacity of the terminal.
A third expansion further increased the terminal’s capacity in 2015.The innovative design expanded the out-loading bulk materials handling system, including a new berth and shiploader, replacement of the existing jetty, a 2km trestle with linking conveyors and surge bins, and high-capacity roadway. The most significant outcome of the third expansion was the increase in nameplate throughput capacity from 44 million to 55 million tonnes every year without adding to the existing stockpile footprint.
Now 50 years on, Hay Point has three berths and five stacker reclaimers and has processed more than 1.3 billion tonnes of coal.
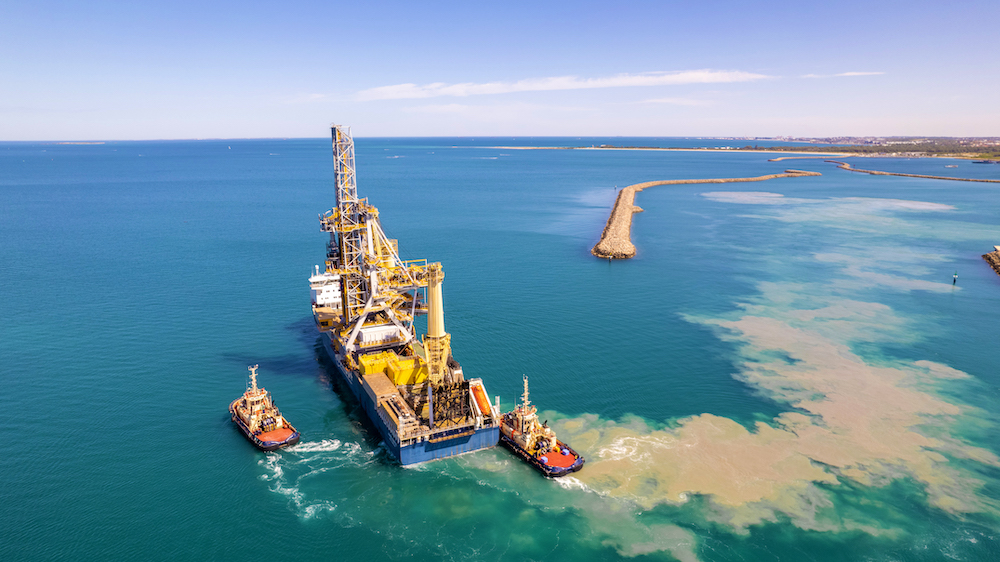
Fabrication by Civmec
The contract awarded to Civmec encompassed the procurement, fabrication, machining, surface treatment, SMP&E, assembly and no-load commissioning of the shiploader.
According to Glen Kovacevic (Project Manager, Civmec), “The project included fabrication of structural platework – we ordered over 1,100 tonnes of plate from BlueScope. It included over 3,000 mechanical items like switch rooms, pulleys, winches, sheaves and pins. This world-class shiploader is one of the largest ever to be built globally and is the largest we have built here at Henderson to date. The boom alone weighed approximately 400 tonnes and was installed via dual crane lift.”
Adopting a national execution methodology, Civmec leveraged their multiple facilities to streamline the fabrication and assembly of the shiploader. Their main Henderson manufacturing facility, located in Western Australia, was used by the team to fabricate all the large material handling equipment. Meanwhile, over 2,000m of handrail, service chutes and special tools were fabricated and surface treated at Civmec’s fabrication facility in Tomago, Newcastle, before being transported to Henderson.
The shiploader was fabricated undercover at Civmec’s newly-built assembly hall at their Henderson manufacturing facility. Final assembly and commissioning were completed at Building 1 within the adjoining Australian Marine Complex Common User Facility. Once completed, the machine was delivered FAS (Free Along Side) to the Australian Marine Complex Wharf for loading onto a heavy lift ship.
“Civmec offered a full turnkey solution to the client. We did everything here – at our facilities in Henderson – so that when they land the shiploader on the wharf, all they have to do is plug it into a power source, and away they go,” said Glen.
“We completed no-load commissioning here onsite as well. We ran all the wheels, drives, and every other component before it got to site. This way, any final adjustment could be carried out before it got it site.”
“It is fantastic that Civmec was given the opportunity to fabricate and assemble the shiploader in Australia.”
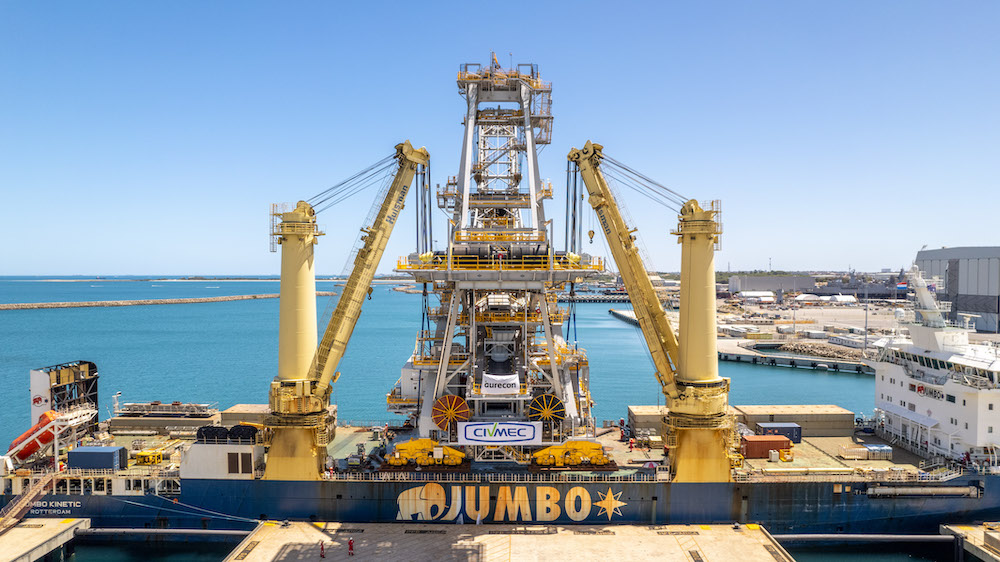
Safety considerations
Civmec’s commitment to health and safety is built on robust processes and a strong culture. Their health and safety systems are certified to ISO 45001, the internationally recognised standard for health and safety management.
In addition, Civmec’s culture is built on the concept of Never Assume, designed to empower every person in the company to ensure their work practices are focused on ensuring no harm to anyone or anything involved in the project.
“The sheer size of the shiploader was incredible. The structure stands at over 52m in height and weighs approximately 2,000 tonnes. With this height, there are extra levels of safety that need to be adhered to, with people working in, around and above one another,” said Glen.
“We spent a considerable amount of time on our methodology input, determining how to ensure that the project was safe for the team to work on, while remaining buildable.”
“The base of the shiploader is just 25m x 25m – a relatively small footprint, given all the components that needed to be installed within. When it came time to assemble the shiploader, we had electricians, piping and structural, mechanical installation and fabricators all needing to work on the machinery within the same, relatively small footprint. This required significant co-ordination from a safety point of view.”
“The whole shiploader was modelled in Tekla. We used this CAD model to lay out the project before we started fabrication. We were able to see how the footprint would fit in our workshop and plan where and how our team members would work.”
“We liaised closely with the engineering team and had all our welding supervisors and leading hands involved in the planning process to deliver the best possible project outcome. It’s this type of teamwork that makes a major project like this one successful,” said Glen.
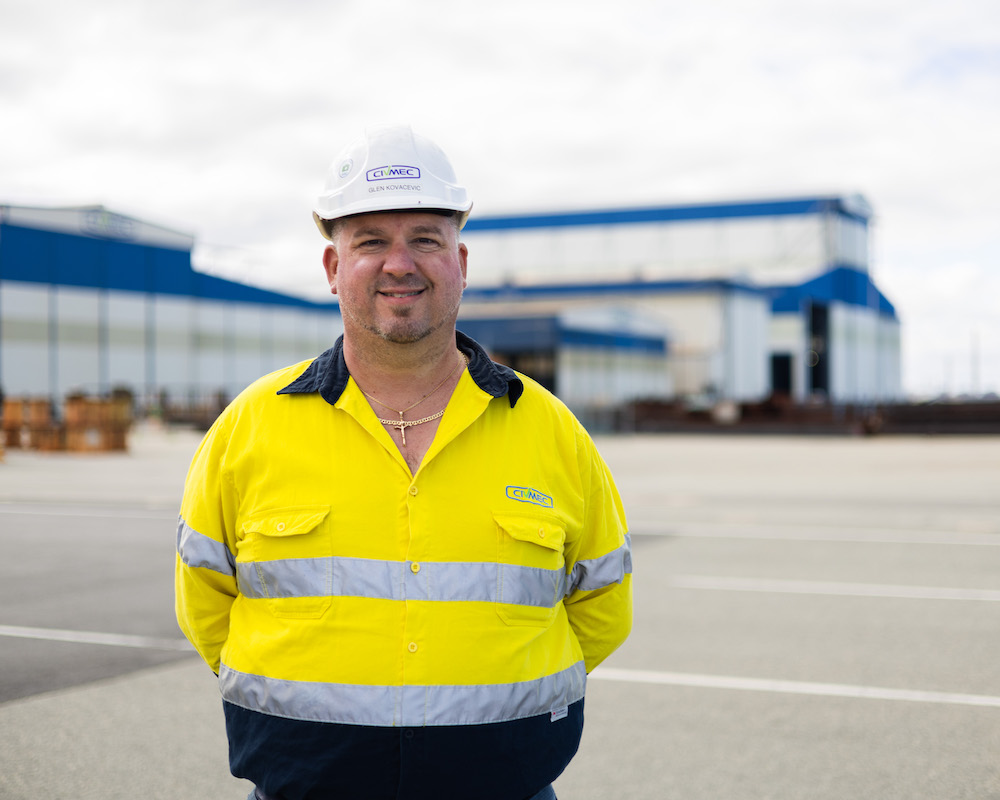
Innovative methodology
Providing quality products and project outcomes for clients continues to be a fundamental metric of success for Civmec. Their facilities in Perth and Newcastle hold CC3 certification to the requirements of AS/NZS 5131 Structural steelwork – Fabrication and erection. Civmec has also obtained certification to AS/NZS ISO 3834.2 Quality requirements for fusion welding of metallic materials.
So, it’s no surprise that Civmec’s methodology for this project was highly innovative and firmly focused on safety and quality.
“The way we fabricated the shiploader was different to how it had been done in the past. We thought the process through and were not afraid to make changes to the traditional build method to be more innovative, and that paid off,” said Glen.
“Our aim was to minimise working at heights. So, we did as much work on the ground as possible. We painted the steel on the ground and left weld margins for areas like the mast. We assembled all the walkways on the ground to the mast before we lifted the mast into position. This ensured we had access to the top of the mast once it was lifted into position – this way, there was no need for massive cranes on-site to lift the walkways into place.”
“However, with fabricating on the ground, the usual process is to machine after all the welding is complete. That would have meant machining 50m up in the air due to the height of the shiploader.”
“Instead, we devised a way to fabricate the mast on the ground. We maintained the shape of the mast by using temporary supports and locking pins. At the very top where the sheaves are located, we had to weld in a sequence that meant the mast would shrink evenly and maintain the tight tolerance. We had both day shift and night shift surveyors who would check the way the mast was moving when we were welding.”
“This necessitated in-depth input and design from the engineers to minimise shrinkage and maintain the correct tolerances. We undertook extensive pre-weld and post-weld surveying, including employing a third-party surveyor. We used a lot of custom-built jigs and temporary welds so that they could be manipulated if necessary.”
“Our innovative methodology paid off – when it came to assembly everything was within the correct tolerance and fit together perfectly. The hard work upfront paid off and as a result, the commissioning went really smoothly,” said Glen.
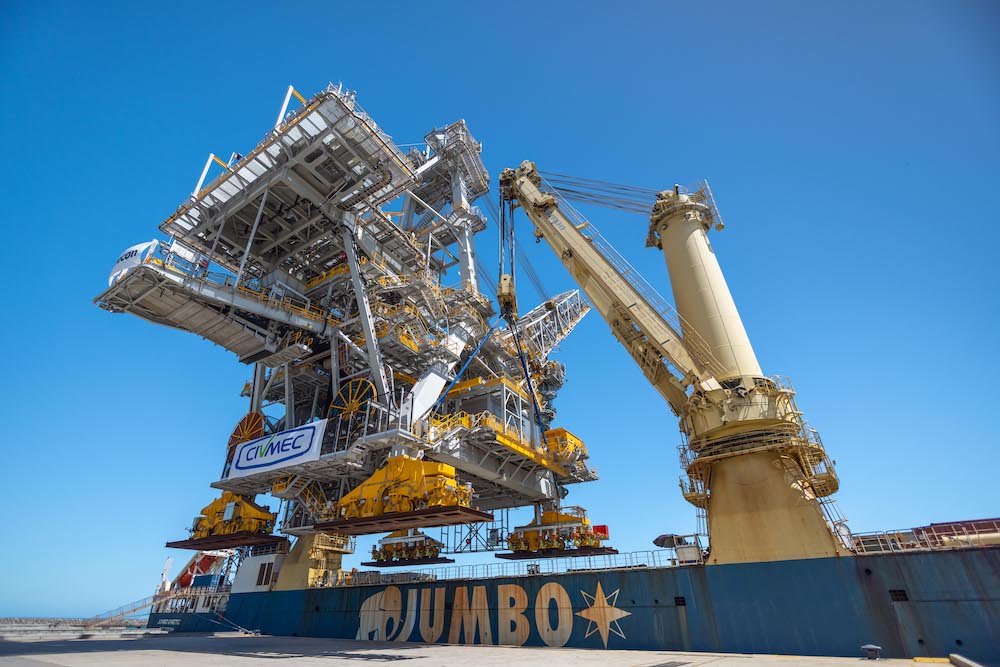
Quality local fabrication
“While Civmec has extensive experience in building Balance machines, this was the first time that Civmec had built this style of shiploader. The feedback we have received from the end users – from the team working at Hay Point Coal terminal – has been fantastic. According to them, the machine is fabricated to a very high-quality standard.”
“It’s great that the client trusted us to fabricate the shiploader locally in Australia, and that we were able to produce a high-quality product on time and to budget,” said Glen.
Project team
- Client: BHP Mitsubishi Alliance
- Engineer: Aurecon
- Steel Detailer: DBM Vircon
- Fabricator: Civmec
- Coatings Supplier: Civmec and International Paints
- Steel Manufacturer: BlueScope
About Civmec
Civmec is a multi-disciplinary construction and engineering services provider to the energy, resources, infrastructure, marine and defence sectors. The company’s vision is to grow sustainably, delivering mutually beneficial outcomes for all stakeholders.
Providing a full turnkey service, Civmec has the flexibility and expertise to improve methodologies, leveraging the synergies of their multi-disciplinary capability to provide clients with cost and schedule efficiencies.
Civmec’s facilities, complemented by their large and experienced workforce and extensive equipment base, enable them to service projects of all sizes and complexities with superior technical, logistical and administrative support. Civmec has worked on some of the largest resources, energy, infrastructure, marine and defence projects undertaken in Australia.
Civmec delivers fabrication projects of all sizes and complexities, with well-equipped facilities and the backing of a highly experienced team. The company undertakes a wide variety of fabrication projects, from structural and platework packages, through to intricate structures requiring specialist welding of exotic materials, such as titanium, stainless steels, duplex steel and copper alloys.
With vast manufacturing facilities, Civmec can deliver platework for a multitude of purposes. Their processing equipment can be optimised for semi-automatic, automatic and user-controlled operability, ensuring consistent quality production and cost-efficient delivery.
Civmec has invested in equipment that can process various grades of steel plate and the company can build large structures in their various bays, the largest sized up to 187m x 420m at the assembly hall, which has an overhead lifting capacity of 400 tonnes.
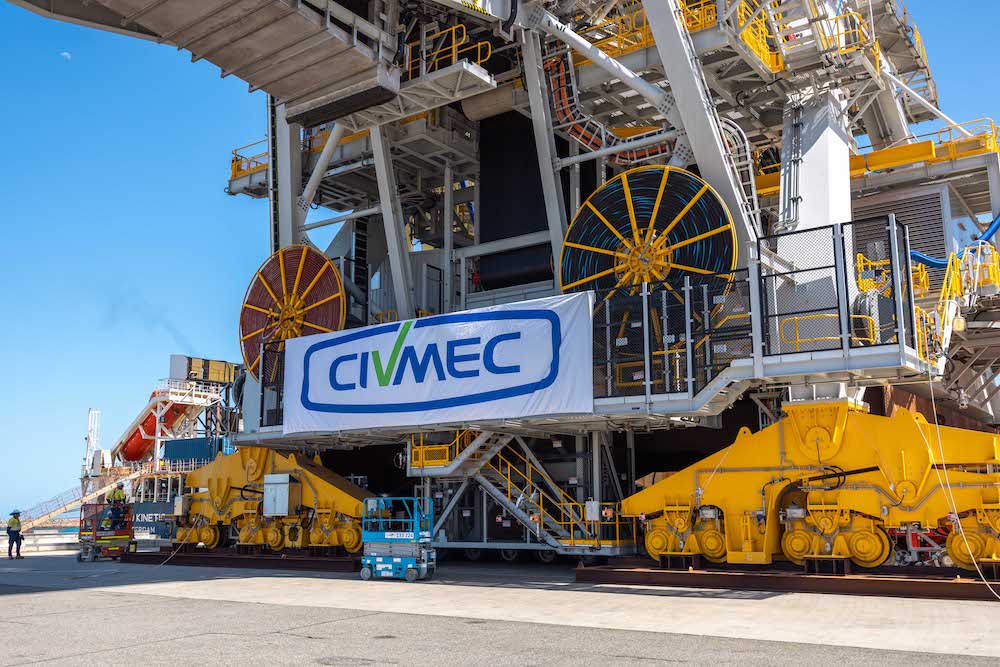