2024 ASI Steel Excellence Awards: National Winner - Engineering Projects
The Hay Point Shiploader – one of the largest shiploaders ever to be built globally – isn’t just a static structure; it is a complex machine with intricate moving parts that reinforce Hay Point’s ability to deliver coal to customers into the future. The shiploader’s completion required strategic planning to address complexity for seamless execution of construction, as well as optimal performance upon completion.
Aurecon’s trade-off studies proposed an acceleration of design and construction to de-risk the project schedule, due to its complexity and possible schedule delays. The methodology involved overlapping workfronts of engineering design, detailing and fabrication.
Utilising parallel direct-to-detail and direct-to-fabrication workfronts minimised risk, improved schedules, and boosted cost efficiency. By integrating Aurecon’s engineering team with DBM Vircon’s construction modelling and detailing team, a single detailed engineering and fabrication model was delivered. This approach enhanced productivity, saved time, and ensured that constructability and crucial fabrication details were considered from the the outset.
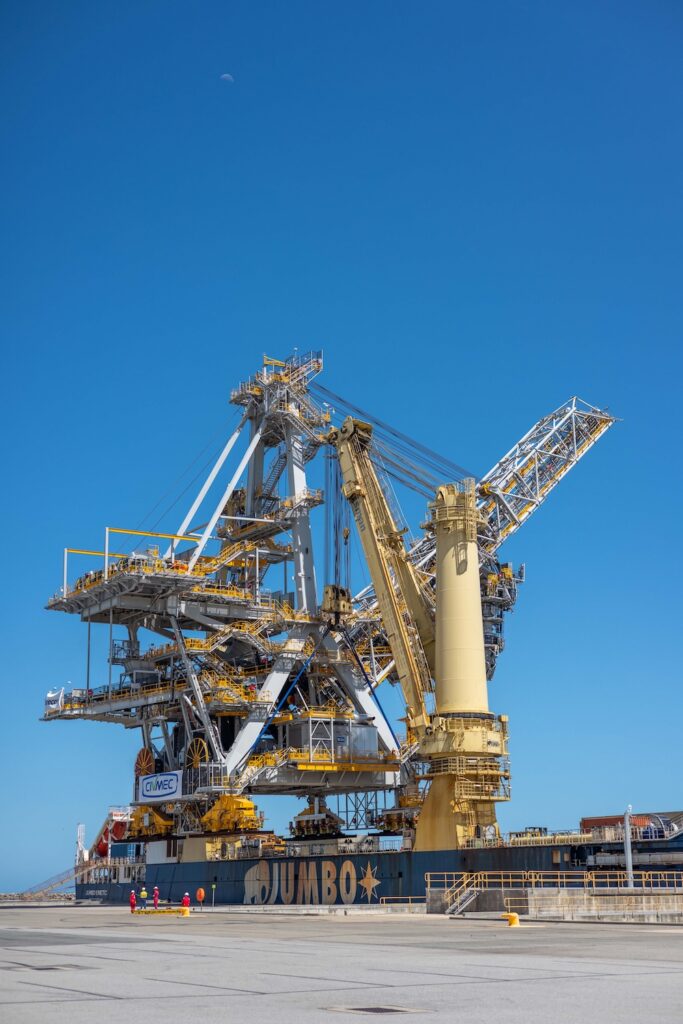
Digital analysis and modelling techniques allowed the design of the structure to consider complex geometries and manage the interfaces between mobile and static structures (such as the shiploader traversing and operating on the berth).
Construction featured in-workshop fabrication of the entire structure, including structural platework and mechanical items, and the use of custom-built jigs and temporary welds to ensure precision. Over 1,100 tonnes of steel plate from BlueScope were used, demonstrating substantial use of Australian steel. Extensive pre-weld and post-weld surveying, including third-party verification, ensured correct tolerances and high-quality assembly. This collaborative and unconventional approach was a success, with the complex machine fully assembled and shipped to the berth on budget and ahead of schedule—despite the project running during the COVID-19 pandemic.
To achieve the shiploader’s on-time completion, modularisation was used to streamline construction, ensuring that shop-built components were assembled efficiently. By fully detailing all services and brackets at the modelling stage, all services could be pre-fabricated and fitted in the shop with confidence that the arrangement would be clash free. The need for development of site-run services was eliminated and disruption to paint finishes were minimised.
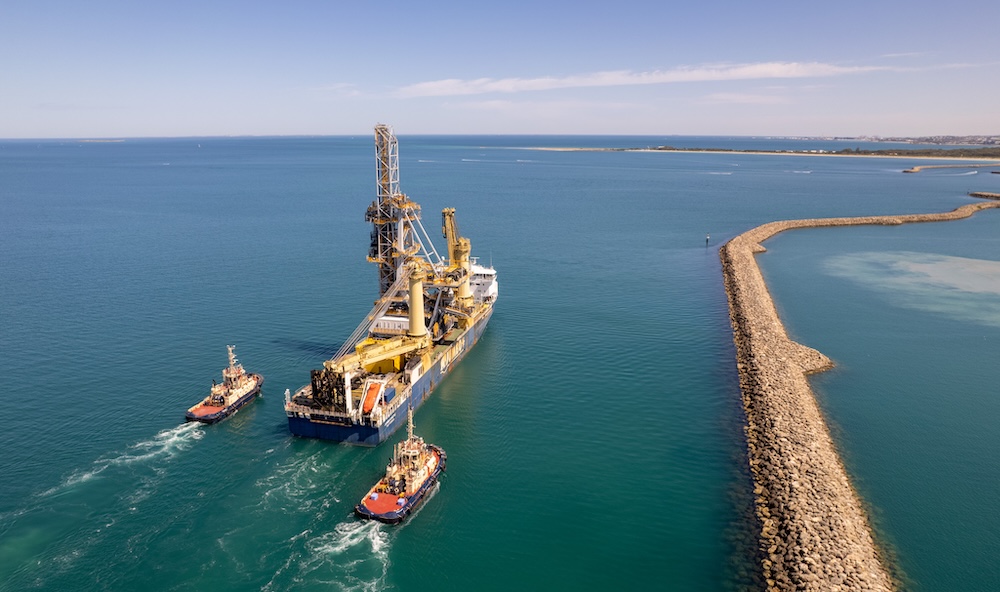
Utilising bolted connections instead of welding for services brackets and modules ensured better control and quality for application of paint, contributing to reduced corrosion, and enhanced longevity and reliability of the machine. Rigorous examination and implementation of dissimilar metals and corrosion isolation strategies were undertaken, ensuring long-term durability and minimised maintenance.
PROJECT TEAM
Entering Organisation: DBM Vircon
Structural Engineer: Aurecon
Distributor or Manufacturer: BlueScope
Steel Fabricator: Civmec
Steel Detailer: DBM Vircon
Coatings Supplier: International Paints