Italsteel is one of Western Australia’s leading producers of steel fabrication products, with proven expertise in the manufacture of complex structural work. A family-operated business, Italsteel provides a full range of specialist services from detailing and 3D modelling, to fabrication and installation.
Italsteel is showing the way for other steel fabricators when it comes to sustainability—with high-quality product delivery supported by ISO 9001, 14001, 45001, SSA L2B and SCA CC3 certification.
General manager Ken Patterson said, “By following the Steel Sustainability Australia (SSA) criteria, we have been able to achieve the outcomes needed by the steel industry for the responsible manufacturing of structural steel and the reduction of carbon emissions.”
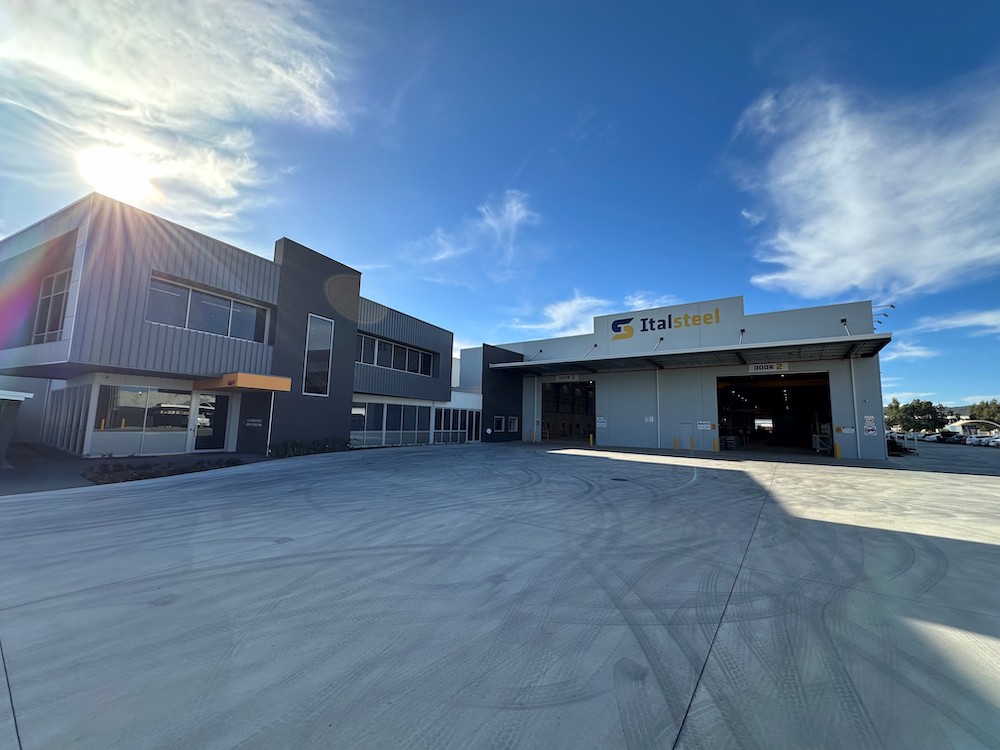
A multigenerational family business
Italsteel was established in 1979 by Alex Gismondi, an Italian migrant who had arrived in Australia with his wife and son in the 1960s. After facing a string of cultural challenges in his work as a boilermaker, Alex decided to strike out on his own.
Starting out in a 1,000 square metre factory, Italsteel grew steadily through the early 1980s and moved to a 2,800 square metre facility. Alex and his son expanded into steel profiling and created Inter Steel. Soon after, this large facility was outgrown. Alex’s son moved Inter Steel into a second factory, enabling both businesses to continue to grow.
In the late 1980s, Alex brought his youngest son Fabio into the Italsteel family as a structural steel detailer and draftsman.
Ken said, “Like all small, family-owned companies, Alex and Fabio did just about everything themselves for a number of years. They ran estimating, design, the workshop, erection—everything.”
By the 1990s, Italsteel had again outgrown its facilities, leading to the purchase of a second building to hold the steel processing equipment.
Today, the company is owned and operated by the father-son-grandson team: Alex, Fabio, and Christian Gismondi.
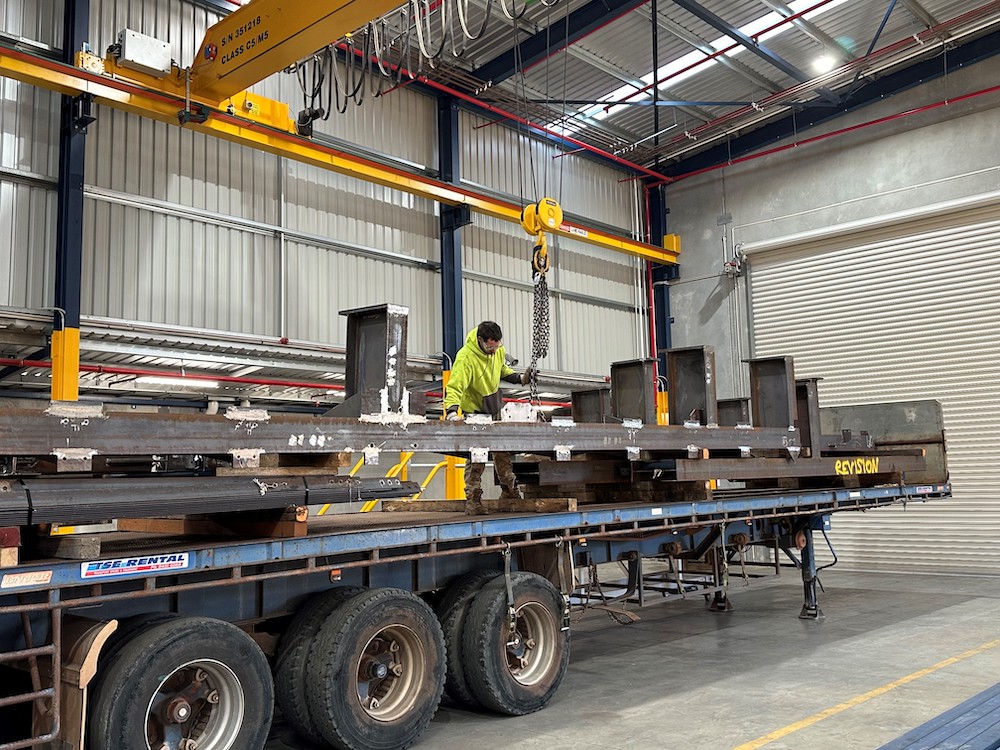
From strength-to-strength
Now almost half a century from its humble beginnings, Italsteel continues to thrive. However, like many other companies, Italsteel has overcome significant obstacles along the way, including the Global Financial Crisis right through to COVID-19.
“During this period, high volumes of work were sent offshore,” Ken explained. “The Gismondi family had to decide either to invest heavily or get out of the industry. The family made the call to invest, and purchased a new facility in Maddington, which is where the company operates from today.”
The facility in Maddington is on a 20,000 square metre property with 11,000 square metres under roof. The factory was in the process of being repurposed when, in 2020, COVID-19 struck.
“Unfortunately, when COVID hit, it slowed everything down so the rebuilding of the factory took a lot longer than we’d hoped. But we were able to occupy the first half of the factory by 2022 and in mid-2023 moved the entire business to Maddington,” Ken said.
“Since then, Italsteel has gone from strength-to-strength.”
With a majority of Italsteel’s clients being from the commercial industry, the business caters for the commercial, industrial and mining sectors.
As Italsteel has grown, so has the size of its clients. “Over the years, our clients have gone from small builders with a turnover of $20 to $30 million a year, to large developers with a turnover in the $200 to $300 million range,” Ken commented.
“Companies like Lendlease are among our largest clients. We are currently completing a couple of projects for Lendlease and the Green Star requirements are a significant part of the project.”
“In the commercial sector, we build factories and a lot of the government schools. All these types of projects have strict requirements, particularly when it comes to Green Star ratings—the government pushes hard for the projects to be as highly rated as possible.”
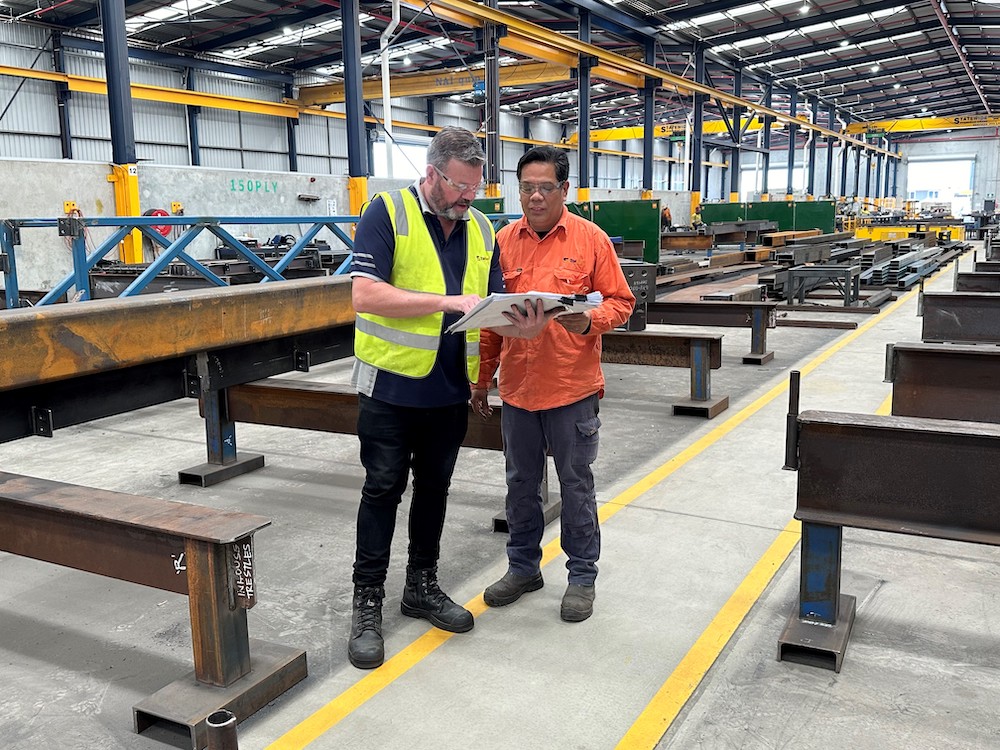
A focus on sustainability
Given the increasing focus on Green Star and sustainability across Italsteel’s client base, the company made a conscious decision that, to move forward as a major player, it would have to be accredited to the key quality, safety and environmental schemes.
Ken said, “What we’re finding is the major developers, miners and government bodies are requiring that companies have SSA certification to help the country achieve our carbon emission reduction targets. In the mining sector, we target work with BHP, Rio Tinto and FMG. As a contractor, you won’t get onto those sites without Green Star ratings.”
In 2020, Ken was brought onboard as general manager to embed a new level of professionalism across the entire operation. Since then, Italsteel has become certified in ISO 9001 Quality management, ISO 14001 Environmental management systems, ISO 45001 Occupational health and safety management systems, Steel Sustainability Australia (SSA) L2B and Steelwork Compliance Australia (SCA) CC3, implementing best practice sustainable operations in the entire steel value chain.
The SSA program verifies upstream raw steel manufacturing mills and certifies downstream steel businesses such as distributors, fabricators, roll formers, and reinforcing processors, against best practice environmental, social and governance (ESG) indicators.
“It was a conscious decision by Italsteel that to move forward as a major player, the company would have to be accredited to the major quality, safety and environmental schemes,” Ken said.
“By following the SSA criteria, we have been able to achieve the outcomes needed by the steel industry for the responsible manufacturing of structural steel and the reduction of carbon emissions.”
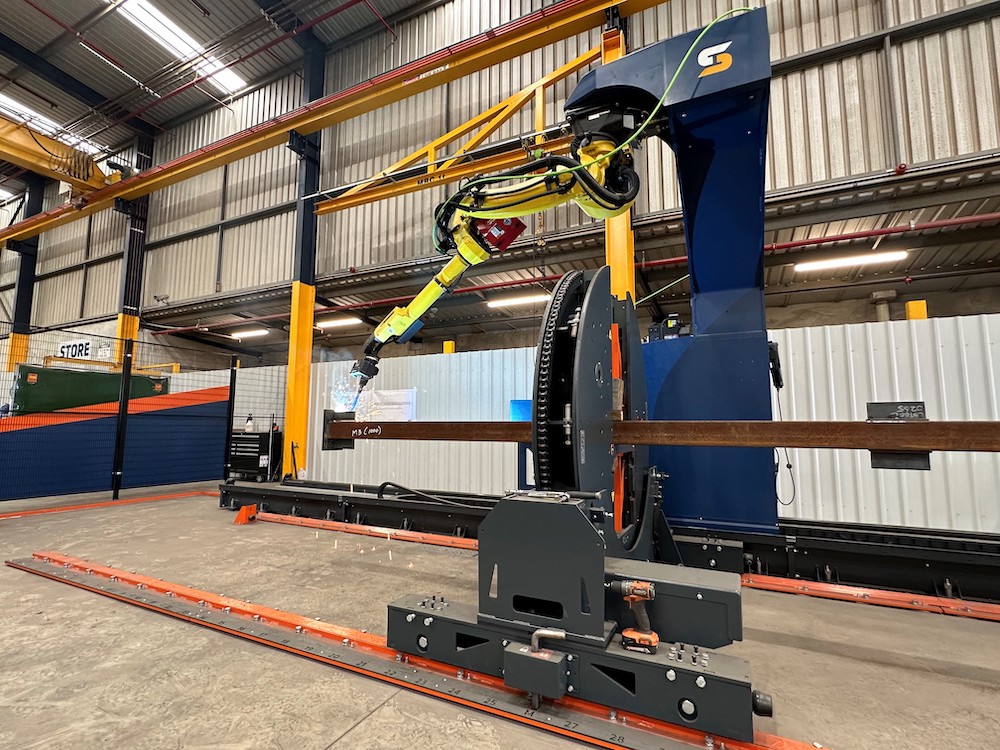
Becoming a low-carbon leader
Italsteel has become an industry leader in reducing its carbon footprint—introducing highly efficient waste disposal processes that have reduced its general and hydrocarbon waste by 50%.
Older equipment has been replaced with modern energy-efficient machines, and more than 90% of its raw materials are now purchased from ACRS-accredited steel mills.
Ken said, “Everything we’ve done here at the new factory has been to manage our waste better, ensure our steel supply is coming from right mills, and ensure our suppliers comply with the Modern Slavery Act requirements.”
The business is also currently in the process of installing solar panels to allow the use of renewable power sources for its operation, which is expected to reduce its reliance on traditionally generated power by 70-80%.
According to Ken, having accreditation under the ASI’s SSA certification program has enabled Italsteel to build relationships with larger companies looking for responsible suppliers. By delivering a robust framework for reducing its carbon footprint, it ensures that all efforts are correctly and directly aligned with sustainability targets.
“The ASI has really been an instrumental player in both AS/NZS ISO 5131 and SSA certification. Without the help of the institute, I don’t think Italsteel would have met the requirements of either of these standards,” Ken said.
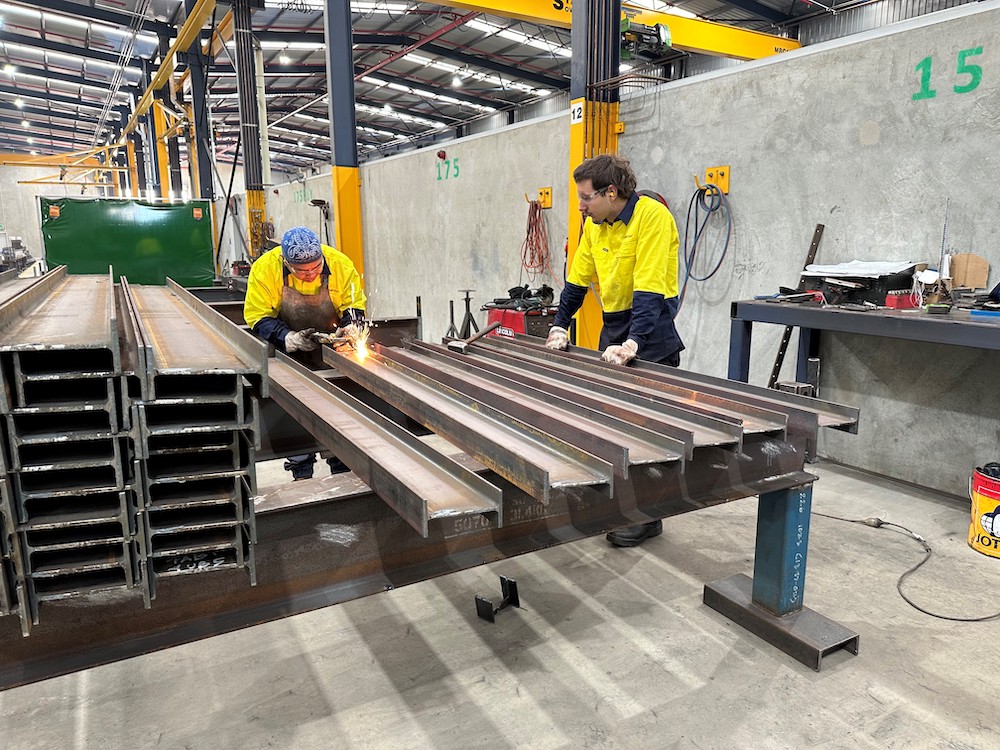