The Western Australia Schools Public Private Partnership Project won the ASI’s 2022 Steel Excellence Award in the Western Australia Innovative Cold Form Steel Buildings category.
The EduWest Consortium and Government of Western Australia (WA) delivered four primary schools (the Woodland Grove, Baldivis Garden, Alkimos Beach, and Carnaby Rise Primary Schools) and four secondary schools (Aveley Secondary College, Coastal Lakes College, Hammond Park Secondary College, and Harrisdale Senior High School) under the WA Public Private Partnership. Lightweight steel was key in the successful delivery of these eight schools; when compared to traditional masonry or brick construction, lightweight steel was cost effective, durable, faster to erect, and much more flexible.
EduWest Consortium’s lightweight steel framed solution for the eight schools responded to the state government’s brief with a built form that is completely innovative. The system provided clear spanning structural framing over internal areas and flexible, non load-bearing internal walls.
This allows for separation of claddings, linings and services from the structural elements in order to generate greater flexibility and adaptability over the lifecycle of the building. Each element can be modified independently of the structural elements meaning that any adaptive works can be done more quickly and cost effectively, with less disruption to the structure, particularly when compared to more traditional construction methods. This will enable schools to confidently respond to factors that drive change such as demographics, technology and learning approaches.
The system also allows for different elements to have differing design life timeframes, allowing each element to achieve its optimum life cycle.
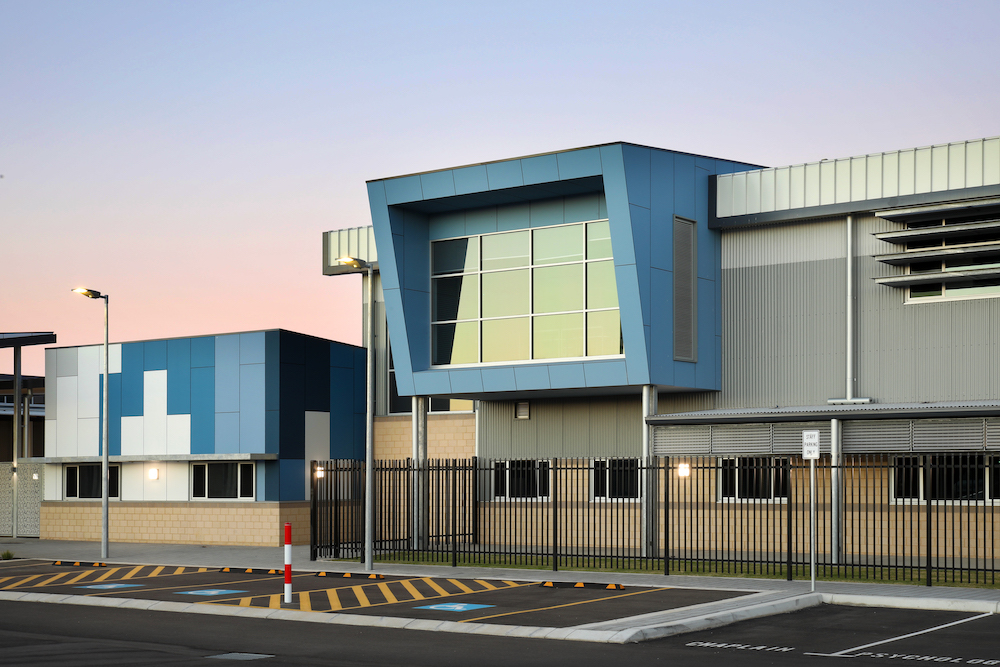
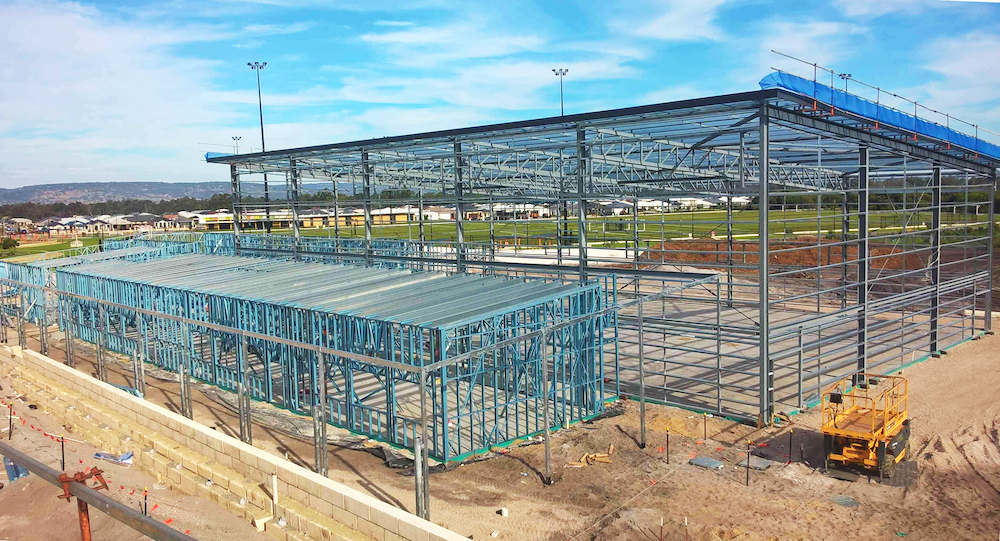
Construction efficiency
The use of light-gauge steel enabled swift frame assembly and installation once the first-floor slabs were poured; reduced the timeline allocated for wall noggins for inbuilt joinery (as they were already incorporated into the framing); and tight tolerances enabled utilisation of split frame internal door frames, leading to a much more rapid fit out.
The system reduced the need for secondary trades to frame out penetrations for tubular skylights or large roof mounted kit, and increased the spacing of supports for soffits, reducing the need for secondary battens to carry external cladding in numerous locations.
This system accelerated construction onsite, with the ability to manufacture major components off-site, to better dimensional tolerances. This improved build-ability, and ensured buildings achieved water tightness much more quickly than traditional construction methods, reducing the likelihood of onsite delays. The simplicity of the construction method and the reduction in materials handling improved onsite safety for workers.
Project team
- Entering Organisations: MODE
- Architect: MODE
- Structural Engineer: Forth
- Head Building Contractor: Badge / Perkins JV
- Distributor or Manufacturer: BlueScope
- Steel Fabricators: Steelscene
- Steel Detailers: Steelscene