The CSIRO Clean Lab won the ASI’s 2022 Steel Excellence Award in the national Steel Clad Structures category.
This project involved the finalisation of the design and construction of a new laboratory for the CSIRO’s Myall Vale Cotton Breeding Research Facilities, which is part of the Australian Cotton Research Institute. The CSIRO specified that the laboratory comply with several industry standards, including Physical Containment (PC2) barrier requirements for the main building. In addition, a separate area within the building had both PC2 and Office of Gene Technology Regulator (OGTR) Invertebrates Performance requirements.
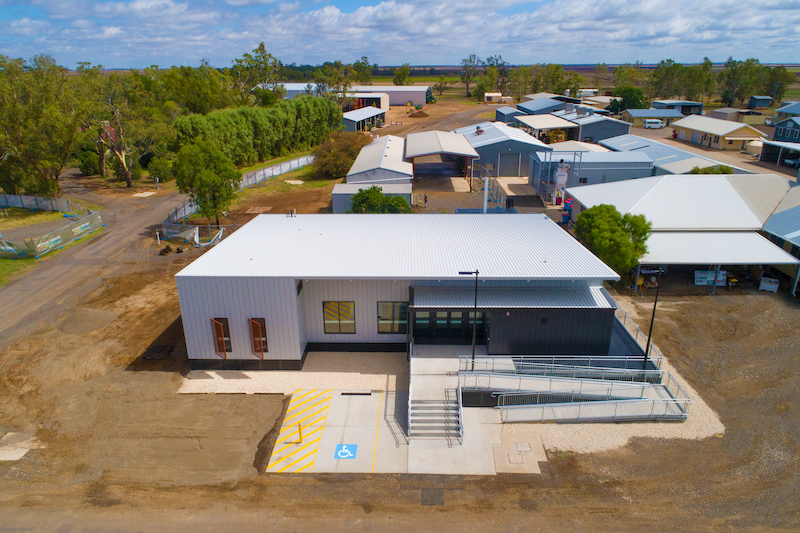
The laboratory was constructed using a non-traditional modular building solution. This solution involved off-site fabrication, with the remaining works undertaken onsite in a similar fashion to traditional construction methodology—all within an operational environment.
The Australian Cotton Research Institute was established in 1972 when CSIRO cotton scientists from Western Australia, the Australian Capital Territory, and Griffith, moved to Narrabri at the heart of the cotton growing industry in the north-west of New South Wales.
The Australian Cotton Research Institute was established to develop new varieties to support a valuable crop to benefit export and the rural economy, and create a farming system that was efficient, sustainable and productive.
Forty years on and the research by the CSIRO team has justified the expectations of those early years: cotton production has grown into one of Australia’s biggest agricultural industries and CSIRO-bred varieties now comprise the entire Australian market including new varieties with improved yield, disease resistance and fibre quality. The variety development is complemented by research in crop management in pests and agronomy as well as delivery of research information in decision support packages.
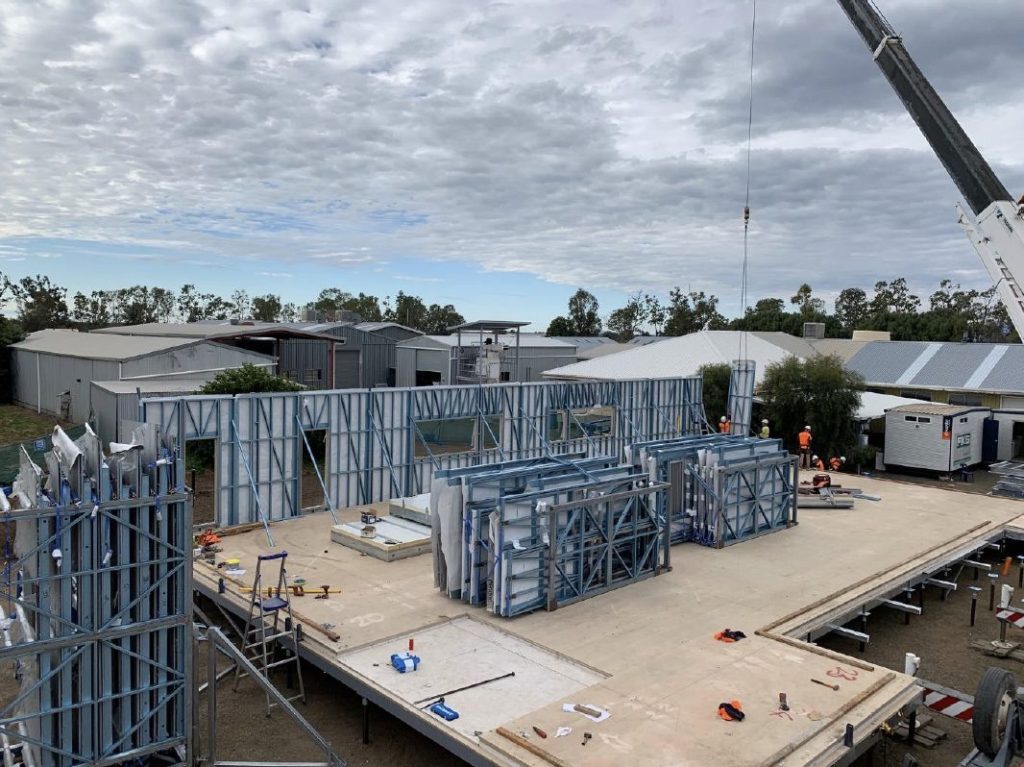
Project complexities
Some of the specific complexities of the project included:
- Laboratory conditions required the building to be air tight
- Laboratory conditions required that the floor have extremely low vibration tolerance
- Wall panels that were up to 6m high required a custom solution for transport and delivery
- The building needed to be easily removed from leased site at the end of lease
Working as sub-contractors to FKG Group, Austruss’ scope of work included:
- Pre-fabricated floor system
- Pre-fabricated light gauge steel wall frames
- Pre-fabricated facade panels clad with Australian steel
- Pre-fabricated roof panels
These elements were all pre-fabricated in the Austruss facility in Braemar, New South Wales and then transported to site for installation. Given the 6m heights of some of the wall panels, Austruss designed specialised systems to facilitate transportation of the pre-fabricated kit of parts.
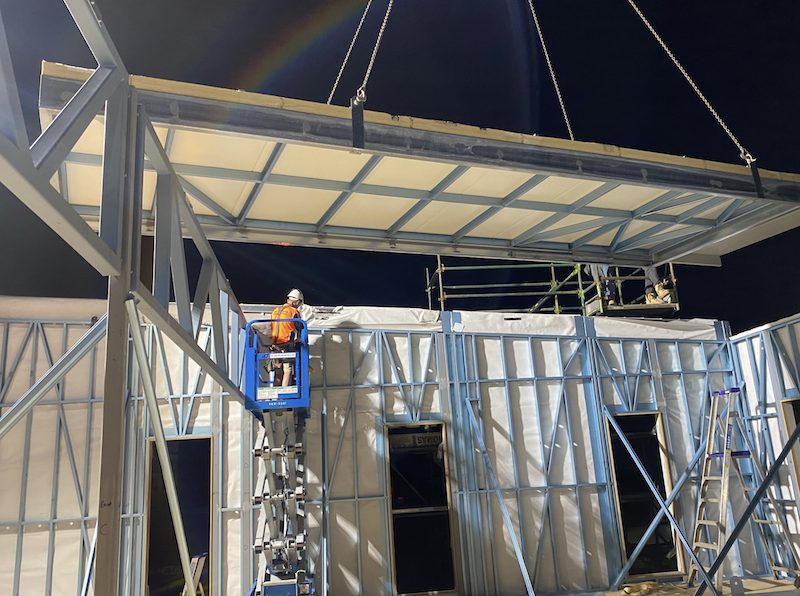
Benefits delivered
Austruss has been a leader in pre-fabricated light gauge steel building solutions since 2003. They provide a customised kit of parts, including wall and roof framing systems, floor cassettes, wall and facade panels, modular construction, skids for data centres and bespoke solutions.
Experts in designing for compliance with the National Construction Code (NCC), the Austruss kit of parts offers competitive advantages, whether by reducing steel tonnage, construction time, trades onsite, truck movements and waste, or impacts of wet weather and site closures.
Key benefits offered by Austruss for the CSIRO clean lab included:
- Limited preliminary site costs, truck movements, disruption, waste and numbers of trades onsite due to most of the prefabrication work happening offsite
- Accelerated project timeline due to parrallel procurement
- Prefabrication allowed certainty and control of build quality
Project team
- Entering Organisation: Austruss
- Architect: L2D Architects
- Structural Engineer: Barnson
- Head Building Contractor: FKG Group
- Steel Fabricators: Austruss
- Steel Detailers: Austruss
- Metal Building Contractor: Austruss
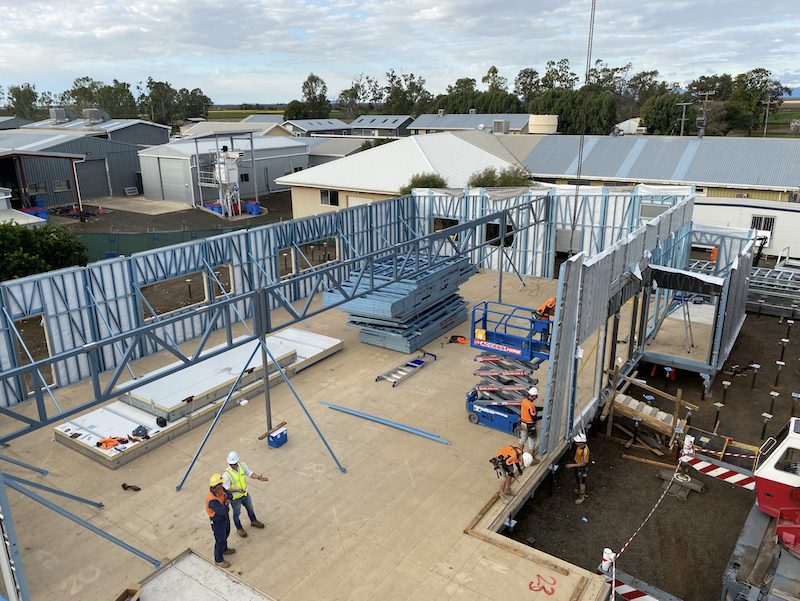