Allianz Stadium won the ASI’s 2022 Steel Excellence Award in the nation Buildings – Large Projects category. The new Allianz Stadium is a modern, world-class venue that will provide Sydney with a sporting and entertainment precinct of an international standard for decades to come. The New South Wales Government invested over $830 million in the development of the new 42,500 seat stadium on the site of the now-demolished original stadium, which was completed in 1988 as one of Sydney’s major bicentennial projects. The new stadium consists of over 5,000 tonnes of Australian fabricated steel through the bowl (seating structure), roof, façade and miscellaneous items.
Allianz Stadium is an iconic and state-of-the-art sports destination located in Moore Park, Sydney. The vision for Allianz Stadium was to blend engineering and art through a ‘sculpture’ and celebration of steel. The project is a legacy for the community that will be enjoyed by generations.
Early and collaborative involvement between the engineer, architect, contractor, fabricator and steel detailer were instrumental in the delivery of this iconic project. Aurecon’s novel industry-leading digital workflow for coordination and collaboration was also critical in achieving the tight two and half year design and construction timeframe—the first steel was ordered in less than three months after commencement of the project.
The stadium was designed with environmental sustainability in mind and is on track to achieve a US Green
Building Council LEED gold rating. The roof structure was re-designed to require 40% less steel compared to the original reference design. The stadium features solar panels and water harvesting systems on its roof, while its carefully designed profile will reduce the building’s overall impact on its parkland location. The roof was even designed to contain noise, reducing noise pollution to the area’s surrounds.
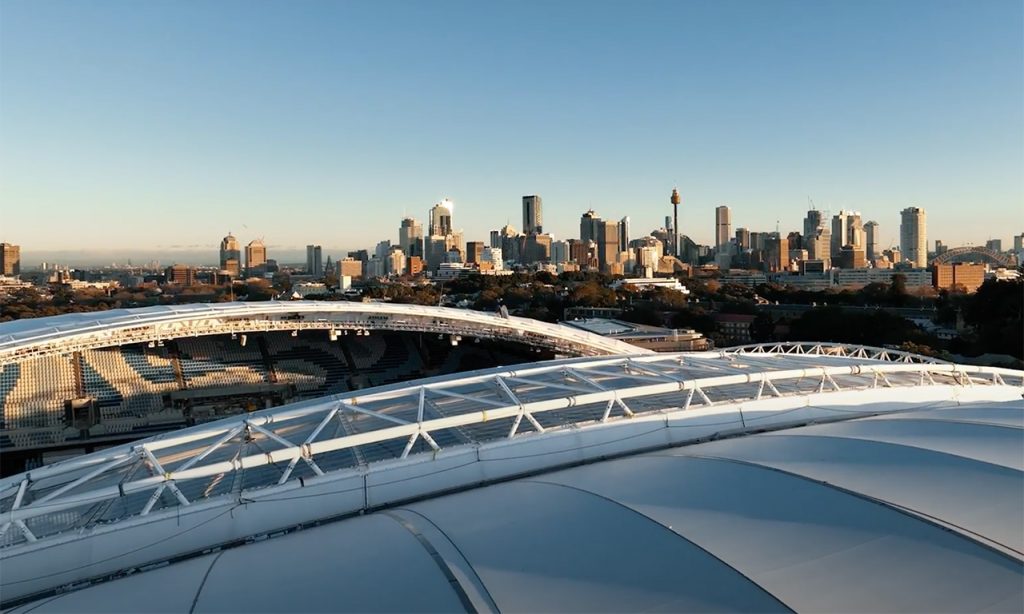
A blend of engineering and art
The design of the new Allianz Stadium builds on the legacy of the original. Its sweeping roof floats over the seating bowl and will cover all patrons with 100% drip line roof coverage. To achieve this result, the 2,000 tonne roof structure is shaped as a synclastic diagrid shell. This is supported by four corner ‘super columns’ (derricks). Spanning between the derricks are inner arched trusses that measure approximately 140m and 90m in length, connected by large 260mm diameter pins. The structural design also includes an outer tension ring and underlying columns that not only support the roof, but connect it to the ‘bowl’ steelwork.
The sweeping roof ‘floats’ over the seating areas, and is lighter than traditional stadia, using up to 40% less steel in its construction, and creating a more sustainable project, while still covering every seat in the stadium and providing fans with clear views of the playing field. The roof form and geometry results in one of the most technically complex stadia roofs in Australia, with 4,000 individual pieces of steel, each with a pre-set length and geometry.
Connecting each roof element precisely onsite with accurate fabrication required digital engineering techniques to model the entire roof geometry for multiple stages of construction.
The connections within the roof sculpture, which are all exposed, became some of the most intricate in Australia; sophisticated bi-directional digital workflows between the structural engineers and steel detailers dominated over conventional calculation and coordination methods, saving months in the design and construction program.
The roof was erected in large pre- assembled modules weighing up to 130 tonnes which were prepared on the pitch safely and then lifted into place. This resulted in improved safety—it reduced the number of connections required at height—and improved quality assurance.
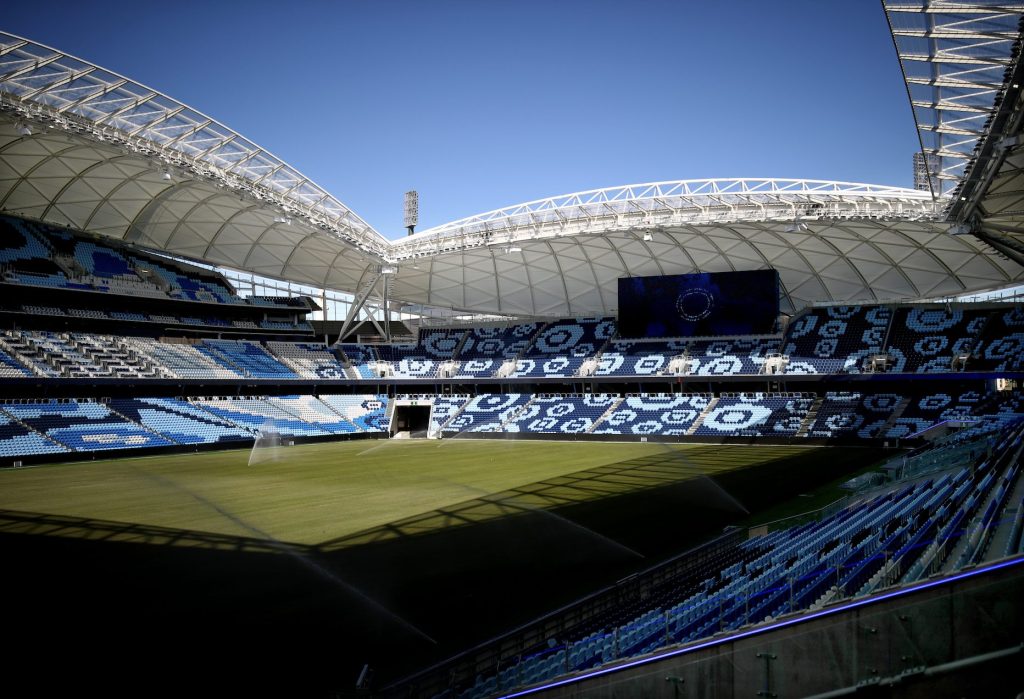
The ‘Pringle’ shaped roof sits atop the coliseum like ‘bowl’ steel structure, which simultaneously supports the pre-cast tiered seating for 42,500 enthusiastic cheering fans. The rakers which support the seating bowl consist of long-span welded open sections procured and fabricated in Australia. Complex assessments were required for dynamic human loading, such as the famous Sydney Football Club Poznan, the team chant in which the fans jump up and down in unison. Over one million dynamic simulations were performed to ensure compliance with one of the most onerous client dynamic briefs ever imposed with any Australian sports stadium.
A sculptural, ribbon facade draws on elements of technology, engineering and art. Covered in a delicate veil of bronze fins, the façade forms an environmentally responsive skin that enhances patrons’ sense of connection to place. Through variations in density and visual porosity, the veil reveals internal programmatic intensity, screens pragmatic functional zones, curates significant external views and connects the seating bowl to the park. The new stadium will have substantially improved sightlines—there will not be a bad seat in the house.
The atmospheric corrosivity category for the stadium is C3 to AS/NZS 2312.1 and the design life of the structure is 50 years. The three-coat protective paint system for the stadium steelwork has been selected to achieve a massive 25+ years life to first maintenance warranty with all sharp edges or welds rounded to ensure an appropriate application is achieved. Closed sections have generally been adopted in non-wash down external areas or adverse micro-climates within the stadium to minimise the exposed surface area of the steel, and to reduce the potential build-up of sulphates, chlorides and other organic material which typically accelerate the rate of corrosion.
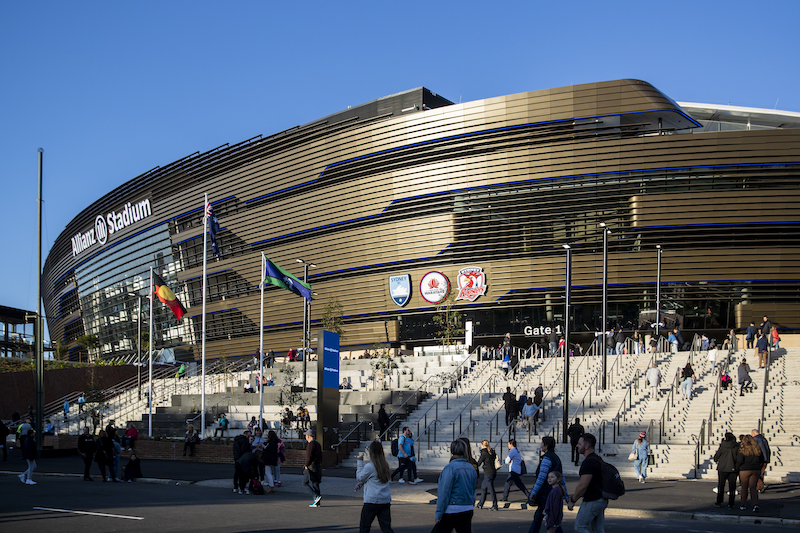
Fabrication of the roof
The roof structure was detailed and fabricated in a way that it was doubly symmetrical. Items such as the diagrid nodes, for example, were very complex with 528 unique instances of connections geometries and details proposed in the reference design. Hence, Aurecon’s design decisions, such as adjusting the geometry of the roof, which had no axis of symmetry in the reference design to a structure that was doubly symmetric, created repetition and reduced the shop detailing effort to improve efficiency and quality assurance.
The choice of fabrication methodology enabled the same section profiles, welding setup, and additional flexibility in the fabrication and installation sequence. Collaboration between Aurecon, COX Architecture and DBM Vircon enabled computational engineering techniques to be adopted for the design and detailing of the connections, which simplified the 528 connections into only five connection types for the entire roof diagrid.
S&L Steel, both SCA and ESC certified, was awarded the contract to fabricate the complex roof structure, which consisted of a tension ring located on the outside perimeter of the roof, four derricks which support the roof in the four corners and four trusses broken into ten liftable sections which are complemented by the diagrid structure being a combination of RHS, CHS and plated node connections.
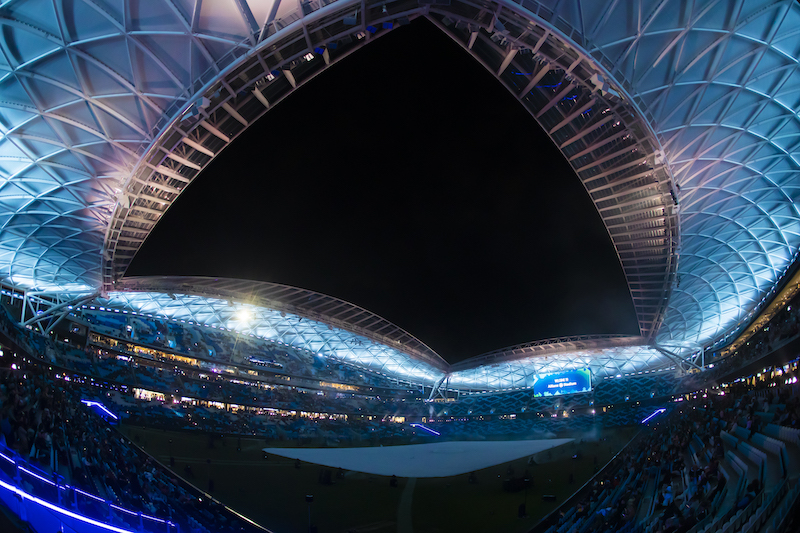
Procurement consisted of primarily circular hollow sections (CHS) up to 762mm in diameter and 400x200mm rectangular hollow sections (RHS) members with plate supplied locally by BlueScope. The process of procurement took over 12 months and was staged to align with lead times and the critical path for erection, all steelwork was validated with NATA and ILAC accreditors. Approximately 18km of material was procured for the 2,000 tonne roof structure. Processing of the CHS sections was undertaken at KMAR Engineering.
The new Allianz Stadium strengthens Sydney as a destination for major sporting and entertainment events while enhancing the surrounding precinct with public places and spaces year-round. The project was delivered on time and on budget by more than 7,000 personnel, despite disruptions to procurement and construction due to COVID-19, a proud achievement for the entire design and construction team.
Project team
- Entering Organisation: Aurecon
- Architect: COX Architecture
- Structural Engineer: Aurecon SBP
- Head Building Contractor: John Holland Group
- Distributor or Manufacturer: BlueScope
- Steel Fabricators: S&L Steel, Samaras Group
- Steel Detailers: DBM Vircon, van der Meer
- Coatings Suppliers: International Paint, Dulux
- Metal Building Contractor: Permasteelisa
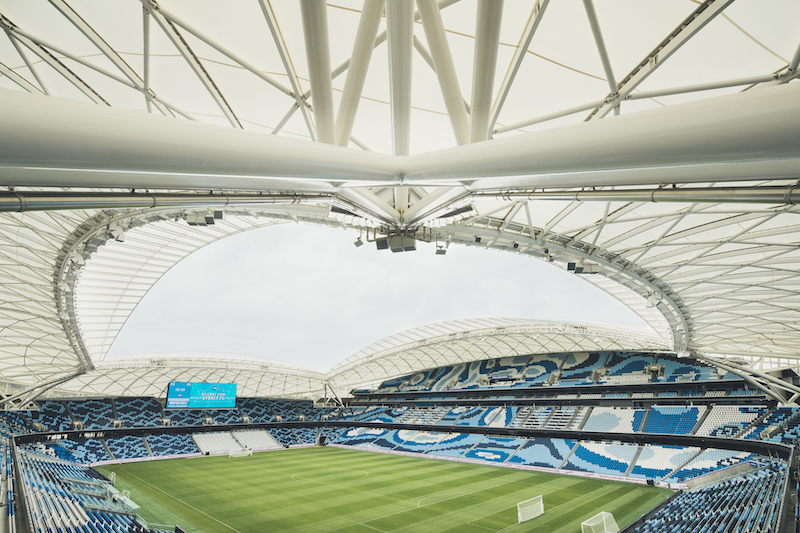
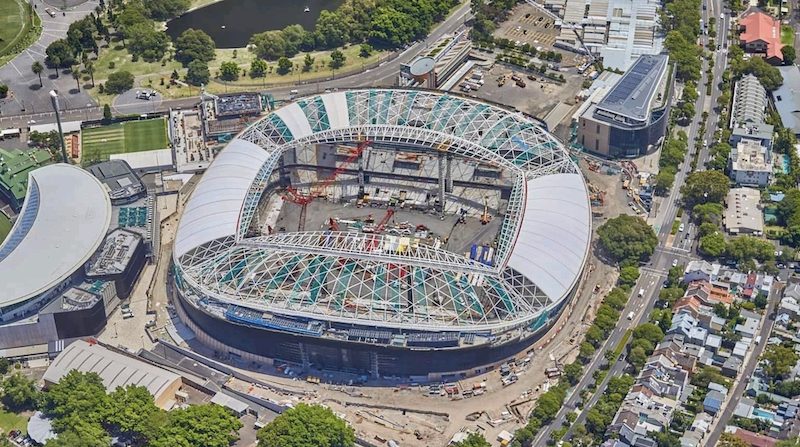
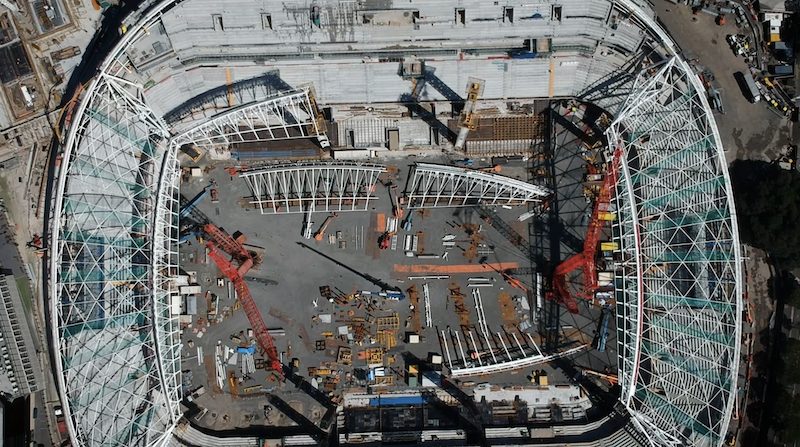